TRYON BLOG
13 Burning Questions for a Pioneer in Warehouse Modernization

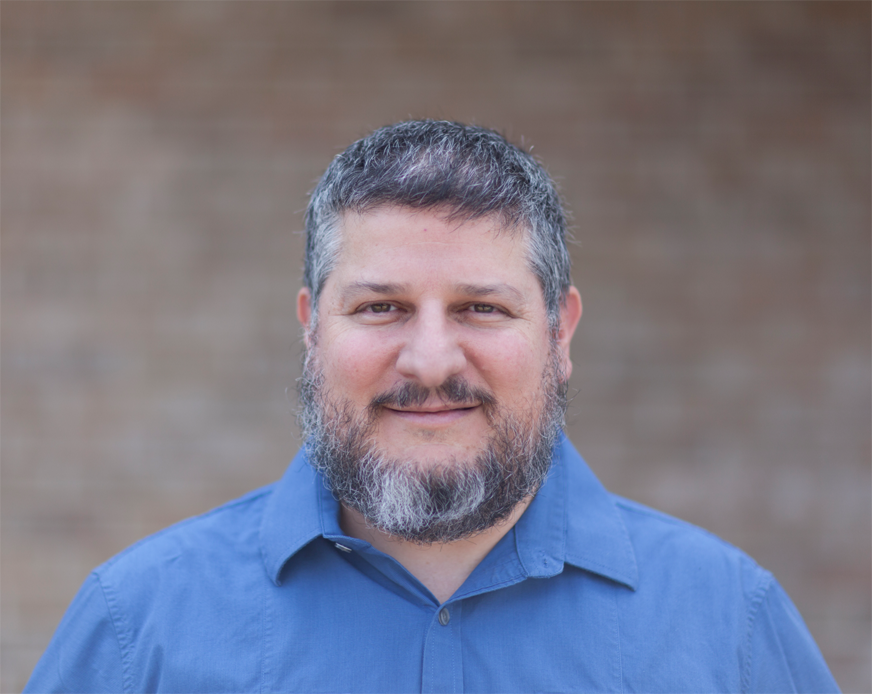
Trevor Blumenau is a professional engineer with a master’s degree in robotics from UC Berkeley and has 25 years of R&D experience in warehouse/manufacturing processes, controls, and innovation. Trevor founded Voodoo Robotics to modernize warehouse operations by leveraging modern technologies.
Voodoo’s first product, a next-generation Automated Storage and Retrieval System (ASRS) includes a web-based, real-time 3D interface and sophisticated modeling built in WDL, a Warehouse Design Language he invented. For companies not yet ready for full automation, Trevor designed and built a wireless Pick-to-Light system based on the Industrial Internet of Things (IIoT). He also founded a company called NuWeb, where he invented the foundational technology for all internet advertising measurement, and that was subsequently acquired by Nielsen Media. Trevor is able to imagine and then create technology that revolutionizes whole industries and with Voodoo’s technology and over fifty patents to his name, he is both a proven innovator and a pioneer in the order picking space.
1. What drew you to the supply chain space, and warehouses in particular?
My interest in the supply chain and warehouse sector stemmed from a blend of curiosity and a desire for improvement. With my background in engineering and robotics, I was naturally drawn to optimizing complex systems. Warehouses, central to supply chains, presented an opportunity for impactful enhancements. The outdated technology prevalent in many warehouses was a significant motivator for me. I saw the potential to revolutionize these spaces with advanced solutions, overcoming the industry’s resistance to change. My goal was to demonstrate the substantial benefits of modern technologies in increasing efficiency and modernizing traditional practices. This fusion of problem-solving and innovation ignited my passion for this field.
2. From what you’ve seen in recent years at warehouses and distribution centers, what single area deserves the most focus and improvement?
The most critical area for improvement in warehouses and distribution centers is labor management, particularly in enhancing efficiency and accuracy. Labor costs comprise about half of warehouse expenses, indicating a significant opportunity for optimization. The focus should be on enabling staff to work more intelligently, leveraging advanced technology to speed up and refine tasks. Modern technologies can guide workers more efficiently, minimize errors, and ensure optimal productivity. Many warehouses are still relying on outdated methods, missing out on substantial gains in productivity and accuracy. Implementing contemporary solutions like Cloud Display Devices can revolutionize worker interactions, easing their workload and significantly boosting operational efficiency. This approach benefits both the workers, who experience less stress and increased productivity, and the warehouse operations, which become more cost-effective.
3. What is the most promising trend you’ve noticed in our space, and what is the most concerning?
The most promising trend in our industry is the integration of Artificial Intelligence (AI) into warehouse operations. AI, exemplified by tools like ChatGPT, offers more than mere task automation; it introduces a level of intelligence and adaptability that can transform warehouses into smart, self-improving environments. Combining AI with Cloud Display Devices and other IoT technologies promises to enhance efficiency, accuracy, and operational agility, making warehouses not just storage and sorting centers but dynamic, learning spaces.
Conversely, the slow adoption of these technologies in many warehouses is concerning. Reluctance to adopt AI and IoT stems from a fear of the unknown and the investment required. This hesitation isn’t just about missing out on new technology; it risks lagging in a rapidly advancing industry. Warehouses delaying the integration of AI and IoT might struggle to compete with those utilizing these technologies for cost reduction, improved accuracy, and enhanced service. It’s a pivotal moment for the industry to either embrace change and benefit from it or face the risk of obsolescence.
4. What are the key differences between a standard pick-to-light and the latest version of the Voodoo Robotics pick-to-light system?
The latest Voodoo Robotics pick-to-light system offers significant advancements over standard systems, emphasizing wireless technology, scalability, and ease of reconfiguration. Key differences include:
- Wireless and Scalable: Unlike traditional fixed systems, Voodoo Robotics’ system is wireless, allowing for easy expansion or reduction. Businesses can start small and scale up as needed, minimizing initial investment and easing integration.
- Ease of Deployment and Reconfiguration: The devices, mounted with magnets, can be quickly moved and redeployed, accommodating changes in warehouse layouts and needs. This flexibility is a considerable improvement over the more rigid traditional systems.
- Reduced Investment Risk: The scalable nature of the system allows companies to invest gradually, as opposed to the substantial upfront cost often associated with standard pick-to-light systems.
- Low Maintenance and Long-Term Use: The devices operate on two AAA batteries, with an efficient e-Ink display and custom wireless protocol, significantly extending battery life and reducing maintenance needs.
- Enhanced Functionality: Features like directional arrows aid in accuracy and speed during the picking process. The ability to guide pickers to multiple locations with a single device is cost-effective compared to standard systems requiring separate devices for each location.
- Versatile Display Options: The system supports up to six colors, five lines of text, and can display barcodes or QR codes, adding versatility and adapting to various operational needs.
5. Which KPI in particular should improve post-implementation?
- Picking Speed: The system is designed to increase the speed of picking operations. For example, one customer reported a 66% improvement in picking speed. This increase isn’t just about faster operations; it translates to enhanced throughput and efficiency, positively affecting the bottom line.
- Picking Accuracy: The precision offered by the light-guided system greatly minimizes errors. The intuitive nature of this system significantly reduces the likelihood of picking mistakes, ensuring a marked improvement in accuracy. This leads to higher customer satisfaction, fewer returns, and a better reputation for the warehouse.
Voodoo Robotics Cloud Display Device
6. What infrastructure does the warehouse need to have in place to use your “starter kit”?
To use our pick-to-light starter kit, the infrastructure requirements are minimal, facilitating a straightforward proof of concept:
- Basic Components: The starter kit includes ten devices and a crucial component called a Turbo, akin to a router.
- LAN Connectivity: The Turbo connects by default to our cloud server hosted on AWS–so no local server is required, although we can install a server if the customer requires it. Because the Turbo makes outbound connections, in most cases, no firewall rules need to be adjusted.
7. Does the size or spacing of bins matter?
No. The flexibility of our pick-to-light system makes it suitable for various bin sizes and spacing, accommodating diverse warehouse layouts and inventory types. Key aspects include:
- Adaptability to Different Layouts: Whether the setup involves thousands of bins in a compact area or a more spread-out arrangement, our system can adapt without requiring warehouses to reorganize or restructure their existing bin setups.
- Turbo Range and Support: Turbos, the central connectors for our devices, can support a substantial number of devices (typically 300 to 400) within a range of 75-100 feet. This range can be extended easily by adding more Turbos where needed.
- Automatic Connection: The devices are programmed to automatically connect to the nearest Turbo. This ensures consistent and reliable communication and eliminates the need for manual reassignment or configuration.
8. Could voice picking be used in conjunction with your pick-to-light systems?
Yes, voice picking can be effectively used alongside our pick-to-light systems. This combination is already benefiting several of our customers. Our devices can generate confirmation texts that integrate smoothly with voice picking systems, providing an additional layer of verification and accommodating different operational styles and preferences.
9. What are other interesting use cases for the Voodoo Robotics pick-to-light system?
We have many diverse deployments that go well beyond traditional order picking. Here are a few:
- Manufacturing Process Control: In manufacturing environments, our devices often assist in process control. For example, they have been attached to stainless steel tanks, providing operators with clear instructions on valve operations, enhancing safety, and accuracy in critical operations.
- Logistics and Transportation Guidance: Devices have been used for dynamic signage in warehouses, guiding drivers to appropriate bay doors with blinking lights–particularly beneficial in high-traffic, confusing warehouses.
- Automotive Manufacturing Customization: In the automotive industry, our system is used for customizing specific processes on the assembly line, like indicating paint colors or other customizable features of a vehicle, aiding in customization and quality control. Our devices have also been used for kitting in these environments.
We like to call our devices “cloud display devices”. They are exceptionally adaptable to a wide range of industry needs where clear, timely, and accurate communication is key.
10. How many different warehouse management systems are integrated with your pick-to-light technology?
Our pick-to-light technology is compatible with a wide range of WMS, IMS, ERP systems. For instance, we’ve recently achieved seamless integration with Odoo, an ERP system, which exemplifies our capability to sync with complex management platforms.
The key to this broad compatibility is our technology’s architecture, based on a REST API. This approach simplifies integration significantly. For example, integrating with the Odoo system required only about 500 lines of code, highlighting the ease with which our system can connect to virtually any WMS, irrespective of its complexity.
This simplicity in integration means that warehouses can incorporate our technology without the usual challenges of compatibility or extensive coding. Our goal is to provide a solution that not only boosts operational efficiency but also integrates smoothly into a warehouse’s existing technological framework, thus minimizing disruption and maximizing implementation benefits.
11. What does the near and far future look like for order picking?
In the near future, order picking trends vary by region:
- Europe: A rapid shift towards automation is expected, with AI and robotics becoming central to warehouse operations. This trend is driven by real estate constraints, the need for efficiency and managing higher labor costs.
- Asia: The region is likely to continue with manual processes, presenting a significant market for pick-to-light devices to enhance efficiency and accuracy without full automation.
- Americas: A mix of automated solutions and manual processes will coexist, influenced by cost, labor availability, and specific warehouse needs. This reflects the market’s diversity and operational realities.
In the far future, robots are expected to largely take over order picking as part of broader warehouse automation trends, propelled by advancements in robotics and AI. However, human oversight and decision-making will remain crucial, ensuring alignment with business and market dynamics.
12. How far away are we from large warehouses becoming fully automated?
Achieving full automation in large warehouses is a complex and long-term goal, comparable to the journey towards fully automated driving, as seen with companies like Tesla. This comparison highlights the intricacies and challenges involved:
- Complexity of Warehousing Tasks: Warehouses require mastery over a wide range of tasks, from picking and sorting to handling delicate or irregular items. Each task demands sophisticated robotics capable of adapting and responding with human-like efficiency and judgment.
- Developmental Stage of Robotics: The level of sophistication required in robotics for full warehouse automation is still in developmental stages. We are still several years away from witnessing even small-scale experiments operating reliably, and autonomously.
- Role of Industry Leaders: Amazon’s innovations and investments in warehouse automation are crucial indicators of progress and challenges in this field. Their experiments and developments set benchmarks and reveal practical realities of automating complex warehouse operations.
13. Why has no one invented pick-to-smell?
Well, the idea of pick-to-smell does have a certain… aroma of innovation, doesn’t it? Imagine walking into a warehouse and being guided not by lights or voices, but by the scent of freshly baked cookies leading you to the bakery section, or a whiff of pine guiding you to Christmas decorations. While it tickles the imagination, the reality is a bit less fragrant.
First off, how would we handle competing scents in a busy warehouse? The mix of chocolate, pine, and who knows what else could create a rather confusing olfactory cocktail. And let’s not even think about the potential for scent-based pranks among the warehouse staff!
For now technologies like vision, voice, and light picking are far more practical for the hustle and bustle of warehouse operations. Pick-to-smell will have to stay in the realm of ChatGPT!
Thank you Trevor Blumenau for taking the time to field our question barrage! Our friends at Voodoo Robotics can be found at their website, and if you are debating whether or not you need improved order picking please feel free to drop them a line or alternatively we are easily found here.
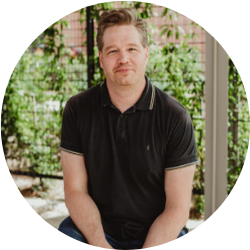
Written By James Prior
With over two decades in software pre-sales and implementation since 2000, James specialized in working with pre-sales teams and contributed to blog posts. For further information, please email sales@tryonsolutions.com.
More From This Category
Key WMS Reports & Dashboards for a Warehouse or Distribution Center
Your company has taken an important step towards the future by investing in warehouse management software. One of the major drivers behind this may have included increasing the operational efficiency of both labor and physical space by harnessing the real-time...
We Saw Robot Picking in Action…
An efficient operation is no longer a “nice to have” in this era of labor shortages and ruthless competition. We recently toured the warehouse of a large electronics company located in the Southern United States that saved 35,000 US dollars a month while increasing...
Top Five Warehouse Management System KPIs
How do we know if our warehouse or distribution center is running as expeditiously as possible? Accounting department touts great numbers, warehouse personnel are clearly working hard, and everything “looks and feels” right, so isn’t that good enough? You...