TRYON BLOG
When to Hire a WMS Consultant

Your Warehouse Management System (WMS) is at the core of your supply chain operations. As the demands on your warehouse evolve, ensuring your WMS is future-proof is critical to maintaining efficiency, meeting customer expectations, and staying competitive. But when is the right time to bring in an outside consultant, and what should they focus on?
Top 8 Critical Times to Bring in Warehouse Systems Consultant
From our customers’ perspective, these are the top times we have been asked to come in and help with supply chain systems.
1. During Periods of Significant Growth
If your business is expanding rapidly, whether through increased order volume, new product lines, or geographic reach, your WMS must scale to meet new demands. An outside consultant can evaluate your current system’s scalability and recommend upgrades or optimizations to handle future growth.
2. When System Limitations Are Hindering Operations
Signs your current WMS might be holding you back include inventory inaccuracies, slow order fulfillment, or difficulty integrating with new technologies. A consultant can assess whether these issues stem from configuration gaps, outdated technology, or process inefficiencies.
3. Before Implementing Automation or Robotics
Automation and robotics can revolutionize warehouse operations, but only if your WMS is equipped to support them. Consultants can ensure your system integrates seamlessly with technologies like automated guided vehicles (AGVs), robotic picking solutions, and AI (artificial intelligence).
4. Preparing for Regulatory Compliance
If your industry is facing new compliance requirements, such as the FDA’s FSMA 204 for food traceability, a consultant can ensure your WMS is equipped to meet these mandates with accurate tracking, reporting, and documentation capabilities.
5. At Technology Refresh Milestones
When your current WMS is nearing the end of its lifecycle or lacks support for modern features like cloud-based operations and AI, it’s time for an upgrade. A consultant can help you evaluate processes, plan migrations, and implement a system designed for longevity.
6. Expanding into New Channels or Markets
New sales channels, such as e-commerce or direct-to-consumer shipping, often require different warehouse workflows and capabilities. A consultant can design WMS processes that accommodate diverse channel needs while maintaining efficiency.
7. Facing Persistent Operational Issues
If your warehouse is plagued by recurring challenges—such as high error rates, frequent stockouts, or poor labor productivity—a consultant can diagnose root causes and recommend solutions. Sometimes a simple, but meaningful system enhancement can be the cure.
8. Planning Major Capital Investments
If you’re budgeting for warehouse expansions, new equipment, or advanced technologies, a consultant can ensure these investments align with your WMS and broader operational goals.
What Should Consultants Focus On?
Bringing in a consultant is just the first step. To maximize their impact, ensure they focus on the following areas:
1. Assessing Current Capabilities
A thorough evaluation of your existing WMS, including its strengths, weaknesses, and alignment with business goals, is essential. Consultants should map current processes and identify pain points.
2. Future-Proofing the System
The consultant should design solutions that not only address today’s challenges but also anticipate future needs. This includes scalability, integration capabilities, and adaptability to emerging trends like AI-driven analytics and IoT devices.
3. Aligning Technology with Business Goals
Technology is only effective when it serves your broader objectives. Consultants should ensure WMS enhancements support your key performance indicators (KPIs), such as faster order processing times, reduced inventory holding costs, or improved customer satisfaction.
4. Streamlining Processes
Beyond technology, consultants should focus on optimizing workflows to improve productivity. This might involve reconfiguring warehouse layouts, enhancing labor management strategies, or automating repetitive tasks.
5. Ensuring Seamless Integration
Your WMS must integrate with other critical systems, such as Enterprise Resource Planning (ERP), Transportation Management Systems (TMS), and customer portals. Consultants should ensure all systems work cohesively to enable end-to-end visibility.
6. Training and Change Management
Technology alone won’t drive results. Consultants should provide training and change management support to ensure your team can fully leverage the upgraded WMS.
The Bottom Line
Bringing in an outside consultant is a strategic investment that can deliver significant returns when done at the right time. Whether you’re scaling up, introducing automation, or tackling operational inefficiencies, an expert’s insights can help future-proof your WMS and drive your business forward.
Ready to take the next step? Contact us to explore how we can help optimize your warehouse operations.
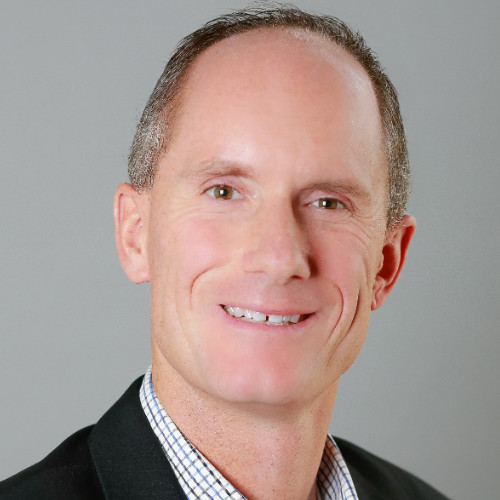
Written By Jeff Constable
More From This Category
Digital Transformation: The Key to Meeting Customer Expectations
In today’s fast-paced retail environment, customers expect seamless experiences whether shopping...
Industry 4.0 Solutions that are Transforming Warehouses
The warehouse industry is transforming with Industry 4.0 technologies, shifting from traditional...
Why Enterprise Software Testing Matters and the Benefits
Software is everywhere in your organization. Design, production, sales, marketing, distribution,...