TRYON BLOG
A Guide to Warehouse Management System Tiers

We’ve defined what a Warehouse Management System is and exhaustively covered supply chain execution acronyms, and so now we must tackle a somewhat nebulous and potentially confusing related subject: Warehouse Management System tier classifications.
What is the difference between a Tier-1 and Tier-2 WMS, and where does a inventory management system rank? Let’s dig in:
Tier-1 WMS
This classification has the most functionality, interconnectivity with other systems, and usually the highest potential level of customizations/modifications. Every single business process from receiving to outbound operations are streamlined and optimized to the fullest, and each area is fully visible thanks to the glut of reporting and dashboards. Large scale warehouses and distribution centers pushing out high volumes often require Tier-1 WMSes to support their warehousing needs. These enterprise-grade systems allow integration with a wide variety of automation equipment, and if you have a special “edge case” process flow they can be tailored to accommodate them – assuming the purchasing department can put the decimal point in the right place both for the tweak itself and the extra maintenance that comes later. The top-level tier of WMSes is the most expensive, takes the longest to implement, and are often very complex to maintain but you can do nearly anything with them. Safely guesstimate that nearly all Fortune 100 companies are running one of the big-league Tier-1 WMS brands.
Example: Blue Yonder WMS
Tier-2 WMS
At this level we have a healthy balance of warehouse management feature-set against cost and implementation time, and generally more configuration than intricate customization. A Tier-2 WMS should also have effectively replaced any residual manual processes for core warehousing workflow operations with (usually, but not always) an easier-to-use interface than the Tier-1 level due mainly to the decreased complexity. Inventory tracking throughout the warehouse is a given, but there should additionally be intelligent features like directed putaway and pick along with related reporting. WMSes in this category are also usually automation friendly and integrate with ERP (Enterprise Resource Management) and OMS (Order Management System) systems. The Tier-2 WMS category is suitable for small and medium-sized operations.
Example: Logiwa Fulfillment Solution
Tier-3 WMS
This relatively inexpensive category offers simple but inflexible warehouse management functionality, and can include ERP or similar systems that have “addon” WMS capabilities. It’s impossible to define exactly which features are stock in all Tier-3 WMSes without choosing a specific vendor/brand, but it’s safe to say that basic tracking should be provided out-of-the-box and any “smart” features – such as telling personnel where to store inventory (directed putaway) or task interleaving – would be a huge bonus. This classification has slim-to-none customization options and so processes workflows must be strictly aligned with the system. Out-of-the box integrations shouldn’t be expected either at this level. A Tier-3 WMS can work for a reasonably small stand-alone storage facility or two, but nothing approaching a busy medium-scale operation and there should be no hint of any omnichannel warehousing needs in the near future.
Example: We don’t have a tier-3 example, so can you think of one? If so, pass it on!
Inventory Management System
An Inventory Management System is a crude “bare minimum” standalone system for inventory tracking that is likely surrounded by legacy processes and endless Excel sheet juggling. It could be built in-house or bought on-the-cheap from a vendor, and can at least reliably tell warehouse managers how much of each inventory type is in stock. Better Inventory Management Systems could also provide where the inventory resides. This barebones system, while probably easy to implement and maintain, lacks the feature-set and robustness for anything other than a small operation with limited inventory serving a niche market that has only a few real competitors.
Example: Joe Bob’s Stock-Wrangler 5000 Pocket App v3.786
How to Choose the Right Solution:
Your team should compile a list of requirements and research solutions that fits your specific needs and size/scale. There are many aspects to investigate, but among the top of the list you should consider what challenges you expect to resolve now and what do you expect down the road. The WMS should also compatible with your existing software (ERP integration is key) and hardware (computers, terminals, etc…), and be sure to research clearly demonstrated real-world ROI against operations similar in size/scale to yours. Don’t simply select a solution (and related tier) based on your current needs…Take the future into account so you can grow into your WMS, as opposed to quickly growing out of it.
Our friends over at Gartner break WMSes up into Leaders, Challengers, Visionaries, and Niche Players. Do you prefer that system, the Tier rankings above, or a combination of the two? Drop us a line and let us know.
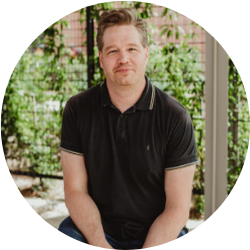
Written By James Prior
With over two decades in software pre-sales and implementation since 2000, James specialized in working with pre-sales teams and contributed to blog posts. For further information, please email sales@tryonsolutions.com.
More From This Category
Beat the Competition on Order Fulfillment Accuracy and Speed in 2024
The demands behind customer order fulfillment speed and accuracy ultimately drives nearly everything that happens in a warehouse. Customer expectations continue to increase in 2024, with no signs of abating in the coming years. Streamlining processes and logistical...
The FDA is NOT FUNNY, But this is…
There is not a lot of funny business when it comes to compliance in the warehouse, but to stay on top of the FDA 21 CFR Part 11 mandate, we’ve added a bit of flavor.1. Know the Rules Like a Super FanImagine the regulation is your favorite TV show. Binge-watch,...
Warehouse Management Systems: Origins and The Future
Warehouse management systems have come a long way from the humble origins of a simple inventory list in green text to a complete, sophisticated system that orchestrates the optimized movement, storage, and retrieval of inventory with detailed reporting at every stop....