TRYON BLOG
Fun With Warehouse Management Acronyms: Differences Between WMS, TMS, WLM and OMS

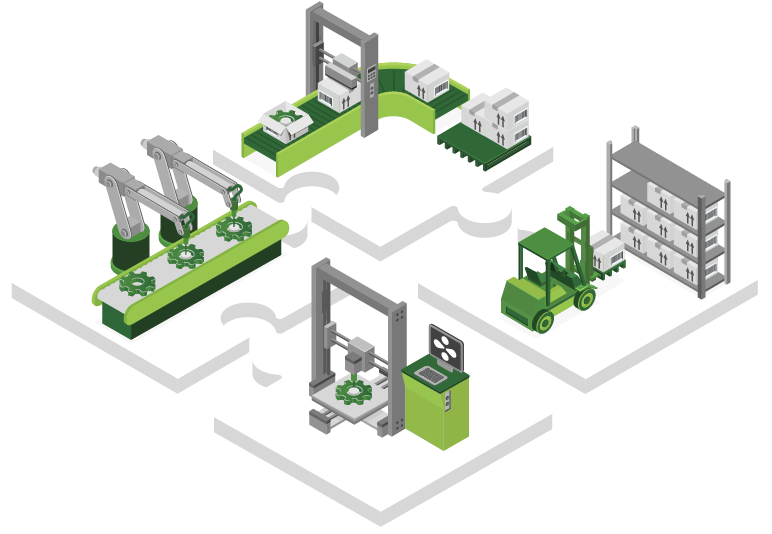
There are acronyms galore in the supply chain execution world ending in “System.” The sheer amount can be confusing, and so can the relationship between them. It is critical that each are properly interfacing and working in concert together to ensure that your operation is maximizing the benefits of these systems.
There will be plenty of overlap, but for whatever assortment that your warehouse is currently leveraging or debating using in the future, think of these systems as puzzle pieces that must properly fit together. Let’s first understand what these acronyms mean and how they work in conjunction with your WMS.
WMS – Warehouse Management System
The core functionality of a WMS is to help manage and streamline day-to-day operations in a warehouse or distribution center, and “guide” inventory through receiving, put-away, inventory management, picking, and shipping while optimizing these processes and advising on inventory replenishment. A WMS is a must-have in today’s ruthlessly, ultra-competitive environment for any medium-to-large business selling a physical product.
We’ve covered WMSes at a basic level and gone over reasons why you may need one, among the many other WMS-centric articles in our “Info Dock” blog.
WES – Warehouse Execution System
A WES organizes and directs the requisite resources (including people and automation systems) required to move goods through a warehouse. A WES interfaces with the WMS to optimize the flow of work that is ultimately needed to ship orders.
NOTE: WCS (Warehouse Control System) has mostly evolved/morphed into WES over time, as a WCS is basically doing the same thing as a WES but is much more limited in scope. A WCS focuses on one or two pieces of machinery, and this can be a problem due to the lack of coordination between areas of the warehouse, but it does not take the overall picture into account like a WES.
TMS – Transportation Management System
A TMS is a logistics platform that helps manage, execute, and optimize the inbound and outbound flow of goods. It can also give visibility into all transportation operations (land, sea, and air), including compliance and documentation, to ensure on-time deliveries. The goal of a TMS is to improve shipping efficiency, reduce cost, and improve customer satisfaction. After a WMS, arguably the next most critical supply chain execution system for a warehouse these days is a TMS. With both a WMS and a TMS, your operation can properly plan and execute the movement of products across your entire supply chain and not just within the boundaries of your warehouse.

Blue Yonder TMS
YMS – Yard Management System
A YMS is designed to orchestrate and optimize the movement of vehicles in the yard – and strictly the yard – of a warehouse or distribution center and gives visibility into trailer locations while allowing them to be efficiently moved from staging areas to the docks.
WLM – Warehouse Labor Management
An WLM efficiently applies performance metrics to human labor to help ensure that productivity targets are satisfied, and provides warehouse managers with handy dashboards for labor forecasting and planning. The overall goal of an WLM is to improve accountability, employee mentoring, and properly inform any labor-related management decisions. In recent years finding and retaining labor is proving challenging and warehouse managers are not just looking to automation for relief, but also WLM systems.
OMS – Order Management System
An OMS automates the management of orders along with all the billing-related details throughout their entire lifecycle, from placement to fulfillment. An OMS worth its salt simplifies the process of managing orders while providing visibility into them, and smoothly integrates with your WMS so that orders are pushed through it. Not every company will have a comprehensive OMS, but at the bare minimum there must be a way to create orders.
NOTE: ERP (Enterprise Resource Planning) systems often include OMS functionality, but covers much more broad and integrated management of the overall core business.
Here is a handy acronym cheat sheet that covers the entire supply chain execution alphabet soup. Do you need some help “making the pieces fit” between your supply chain systems? If so, please drop us a line!
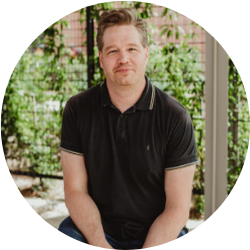
Written By James Prior
With over two decades in software pre-sales and implementation since 2000, James specialized in working with pre-sales teams and contributed to blog posts. For further information, please email sales@tryonsolutions.com.
More From This Category
Why Would You Need a Labor Management System?
Delivering a product to the right place at the right time efficiently can take more than just having a Warehouse Management System (WMS) in place. In today’s ultra-competitive environment, which includes an uncertain labor market, your warehouse must fully maximize...
13 Burning Questions for a Captain of WMS Industry: Erhan Musaoglu
We’ll now be interspersing "Burning Question" interviews with experienced WMS professionals and industry leaders into our “Info Dock” Blog, and to kick-off our interview series we scored the latter with a true captain of industry in the WMS space: Erhan MusaogluErhan...
Why Would You Need a Transportation Management System?
Delivering a product to the right place at the right time can require more than just a system that optimizes everything within the walls of a warehouse, and so let's answer the question: Why would you need a Transportation Management System? Meeting customer service...