TRYON BLOG
Why Would You Need a Labor Management System?

Delivering a product to the right place at the right time efficiently can take more than just having a Warehouse Management System (WMS) in place. In today’s ultra-competitive environment, which includes an uncertain labor market, your warehouse must fully maximize the potential of your workforce.
You can drastically improve your chances of doing this by implementing and properly using a Warehouse Labor Management (WLM) System. Labor can be measured, managed, and planned just like anything else at your warehouse or distribution center.
Key Benefits of a Warehouse Labor Management System
- Better training, coaching, and performance related incentive programs
- Improved workforce visibility
- Optimized work schedules
- Properly established labor standards
- Reduced labor related costs
- Improved employee moral
- Improved employee retention
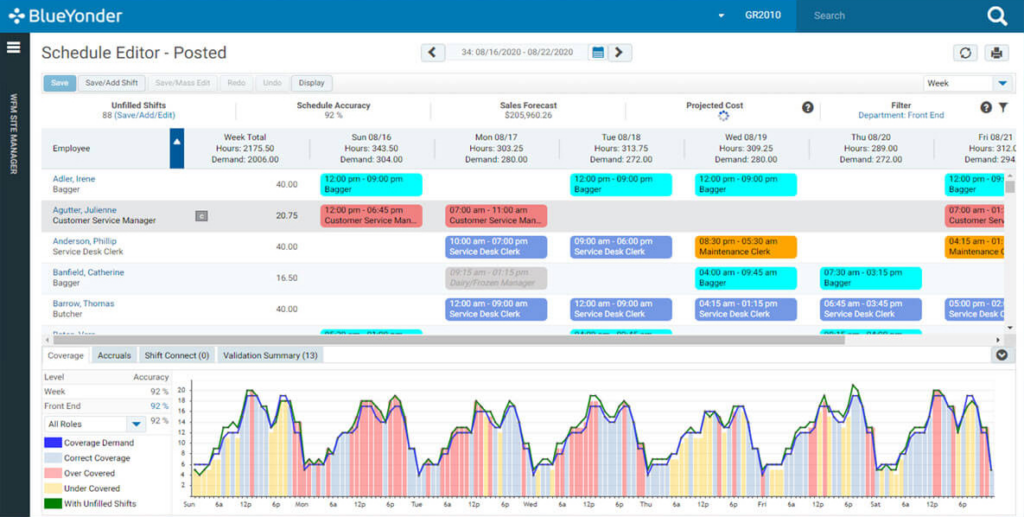
Blue Yonder WLM
Planning and Execution
A warehouse labor management system focuses solely on personnel in the warehouse, and enables the operation to fairly define standards and objectively hold people accountable…BUT there is accountability on the warehouse as well. You can’t blindly order personnel to perform tasks and have unrealistic performance expectations, as the WLM system accounts for them to have proper time to learn their daily standard operating procedures.
While this is a technology implementation, the changes to the operation are more “people focused” than anything involving bits and bytes. With the emphasis being more on the “people” side of the product, robust Change Management measures are encouraged. This is important for the warehouse management team to keep in mind as they prepare for a successful WLM implementation.
Warehouse managers will also need to designate a subject matter expert from the operations and IT sides of the business, as ownership in each area is critical both during implementation and on an ongoing basis.
What other critical ducks should be in a row for a WLM implementation? Workers can only be realistically accountable for processes etched in stone, and so you must have a stable WMS in place along with related stabilized SOP/processes. These processes also need best practices and strict baselines in place. In addition to process standardization, there may need to be a standardizing of the racking layout or other physical layouts. For example, in a newly minted warehouse we should properly establish a golden zone in our slotting strategy before bringing in a WLM.
Analytics
A properly implemented WLM provides a holistic, complete view into warehouse labor. The key WLM analytic is employee/user percent performance for a given task, and it is critical to properly and objectively unpack the stats. Various factors can come into play that affect performance like the user’s reach or seasonality.
If a user isn’t meeting the standard, it is important to find out if there is an extenuating circumstance. Maybe there is something unique about the process which management hasn’t taken into consideration. For example, if the stats reveal they are less efficient in the late afternoon it could be because a taller worker is frequently bending down to reach heavier inventory at the bottom of the rack and so naturally they progressively tire over the course of the day.
If it is revealed that the user has an inordinate amount of downtime, it is important to investigate further to see if maybe they are cleaning their work area or being otherwise productive “outside of the numbers” and not immediately assuming that they are opening cases of whoopee cushions to “test the merchandise”.
Measuring task-per-hour is the old school method; a stopwatch (or hourglass if you are really old school) and a notepad doesn’t take into account how drastically different tasks can be. Treat each task/process uniquely and grade each against its own standard. This means not just how many boxes moved, but how did a user perform to the set standard for that specific box.
Will our employees head for the hills if we implement?
A more productive warehousing operation supports the growth of the business which makes for better job security. Your trusted, valued personnel should also feel appropriately rewarded if you use the WLM the right way and will in-turn be more likely to stick around. Employees that skate by solely on unearned favoritism might head for the hills.
Do I need a WLM?
Is your operation especially labor intensive? Would you like to put an incentive program in place? Are there strict labor compliance rules for your operation? Do you have a WMS and are still striving for better efficiency? If you answered “yes” to one or more of those questions, then be sure to read through this article using it as a primer and of course be sure to check out Blue Yonder and other companies in the supply chain execution space with WLM offerings.
Micro-Level Example Scenario
Replacing the battery on a forklift is a pretty big undertaking, and the time-consuming impact wasn’t fully understood until after Blue Yonder WLM was implemented and the user had the newfound ability to track this “indirect” bucket of time. The previous standard was not taking into account that the forklift operator was also a “battery wrangler” on occasion, and post-WLM big unknowns like that can now be revealed and the user’s day more correctly defined.
Large-Scale Real-World Example
3PL provider DSC Logistics quickly expanded from a single location to over 50 throughout the U.S. After the dust settled from the hurried progress, they realized to have accurate, damage-free, on-time and affordable deliveries a workforce optimization was needed. After implementing Blue Yonder WLM, they saw a 20 percent reduction in labor spend across all sites and improved throughput while gaining a standard methodology for all workers including measurable productivity. They can also now forecast workforce requirements and more effectively schedule based on demand, events weather, and types of automation.
If you are on the fence about adopting a labor management system or need help with your current WLM, please drop us a line! Our labor management consultants can advise on best practices as we review your warehouse map, evaluate process logs, and observe your workforce – and if needed, we’ll make recommendations in the form of an executive summary and configure your WLM accordingly.
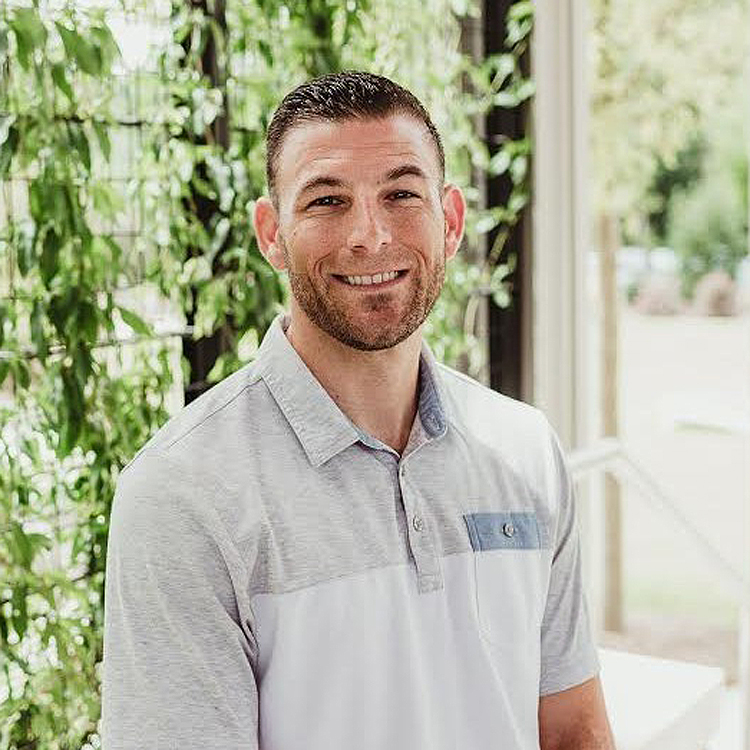
Co-Written By Albert Wimer III
Albert, a Senior Solutions Engineer for Tryon Solutions, has been working with supply chain applications, including Red Prairie / JDA / Blue Yonder suite for 19 years and has gained diverse expertise in this space from his many roles including Logistics Specialist, Business Analyst and Senior Solutions Engineer.
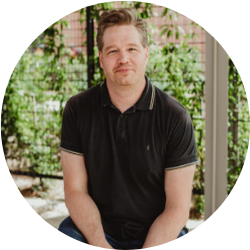
Co-Written By James Prior
With over two decades in software pre-sales and implementation since 2000, James specialized in working with pre-sales teams and contributed to blog posts. For further information, please email sales@tryonsolutions.com.
More From This Category
Why Enterprise Software Testing Matters and the Benefits
Software is everywhere in your organization. Design, production, sales, marketing, distribution, accounting, human resources, legal, customer service, IT, logistics, etc, etc. You name the department, and there will be a software tool that helps manage it....
When Should I Add AI to My Supply Chain Processes?
Adding artificial intelligence (AI) to your supply chain processes can deliver significant benefits, but the timing and implementation depend on several factors. This includes specific needs of your business, the maturity of your existing systems, and the areas where...
A Strategic Move: Building your 2025 Budget for a WMS Update
As we approach 2025, it’s clear that staying competitive in supply chain and distribution requires technology upgrades that can improve efficiency, accuracy, and scalability. A key part of that equation is your Warehouse Management System. Whether you’re looking to...