Use a WMS to Help Calculate Safety Stock
This past year we’ve been seeing warehouses carrying more safety stock to help offset supply chain disruptions. Safety stock is an extra “buffer” of inventory in the event demand increases unexpectedly and/or supply chain issues (like supplier delays, port problems, etc..) prevents you from replenishing one ore more items of inventory. There is a need for this cushion, as “stockouts” result in nearly a trillion dollars in lost sales worldwide every year. Service levels must remain high in our current environment of cutthroat competition, as any real drop-off can negatively affect your company’s reputation. BUT…and we all know there is always a “but”, too much safety stock increases carrying costs and certain types of products (high tech, perishables, etc…) could depreciate in value while gathering dust in storage. Please note that “Safety Stock” is different from “Working Stock”, which is basically the amount of inventory available to meet the expected demand during a specific timeframe.
A warehouse management system helps via:
- A WMS improves the things that you can control, to make it easier to focus on what you can’t
- The historical data behind inventory items can help forecast what is needed for the future
- The overall optimization and accurate reporting of what’s in the warehouse makes it easier to set aside adequate space for safety stock
- A WMS can help fill the variables in your safety stock calculation
Safety Stock = (max number sold per day X maximum lead time in days) – (average number sold per day X average lead time in days)
Let’s try this formula using an actual, real-world situation with a totally realistic product…So your warehouse backs up a Spoiled Egg Flavored Lip Balm outlet located nearby.
Your shop had a great day a few weeks ago thanks to a promotion and sold 137 tubes of balm, and you know that the longest time it would take to get a fresh shipment is 12 days. Now on your average day the store sells around 90 tubes, and the average lead time to get more is 7 days.
Let’s plug the numbers into our formula:
(137 tubes X 12 days) – (90 tubes X 7 days) = 1,014
Your warehouse should keep 1,014 tubes of Spoiled Egg Lip Balm as safety stock
While this formula can help determine an adequate safety stock level, keep in mind that it doesn’t take into account either supplier or logistical reliability. Also, seasonal shifts and – really supply and demand overall – is extremely dynamic these days. We also know that fickle customers could lose their taste for spoiled egg flavoring, and so you will need to keep the above formula up-to-date to maintain proper levels of safety stock.
How do you calculate safety stock? Drop us a line and we’ll compare notes.
This post was written by:
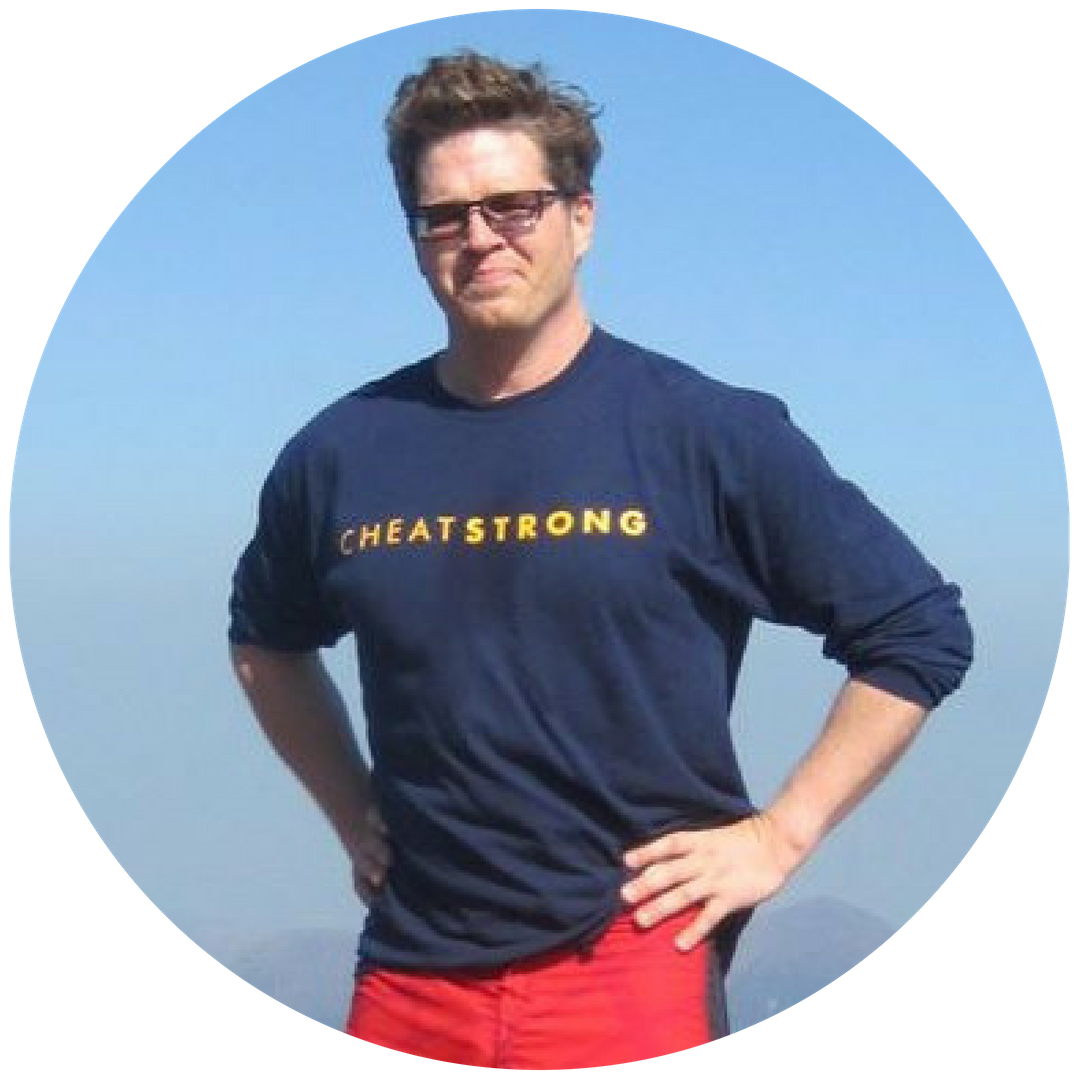
Recommended Content
Fast-Tracking WMS Updates for Regulatory Compliance
Discover how Tryon Solutions quickly delivered WMS updates for regulatory compliance—helping a client avoid fines, meet last-minute French-language requirements, and maintain smooth operations.
Multi-Client Operations and 24/7 WMS Support
In this episode of Rack and Roll: Future Proofing Your Warehouse, we’re diving into 24/7 WMS support—why it matters, how it impacts multi-client environments, and what sets a great support team apart. Join us as we chat with Brian Henry, Director of Customer Care at...
Successfully Upgrading to Blue Yonder SaaS Despite Mid-Project Scope Expansion
This case study explores how our team successfully managed and completed a Blue Yonder SaaS upgrade despite significant mid-project scope expansion. Discover the challenges faced, strategic adjustments made, and best practices applied to keep the project on track,...
6 Levers for Smarter WMS Support
Whether you're juggling school drop-offs, remembering a birthday party, or trying to reply to that one group text before dinner hits the table, modern life pulls us in a hundred directions at once. That constant pressure to keep up, stay flexible, and deliver—no...
Executive Checklist – Is Your WMS Supporting Business Strategy
This executive checklist from Tryon Solutions helps leadership teams assess whether their Warehouse Management System is truly aligned with business strategy. Explore key areas like scalability, customer experience, operational efficiency, and innovation to identify...