TRYON BLOG
4 Compelling Reasons to Outsource Supply Chain Execution Services

Why would one outsource when it’s technically possible to handle everything in-house? I’m a fan of a nice haircut, and I’m willing to pay a little more to get it. Before coming to this conclusion, I tried a well-known super-cheap option out there (rhymes with Supercuts) and left with an uneven cut and a traumatic shampooing experience akin to waterboarding. I also tried handling things myself years ago, and every time I came out looking like a different Stooge. The best route was to pay a little more and outsource my haircut to an expert, and this philosophy translates to the business world as well.
Our company has been contracted on many occasions to rescue a WMS upgrade or implementation going sideways and, in some cases, even to pick up the pieces from a failed supply chain execution project due to the customer believing that they had both the proper in-house expertise and available resources to handle things on their own. It’s good to have people in-house who know your supply chain systems, even at the nuts-and-bolts levels, but they should be working with your vendor to keep them on-track and honest and not spearheading an internal project that takes everyone’s time away from your core business.
Let’s look at four compelling reasons why you should outsource your supply chain execution system services:
- Your top competitor WANTS you to take eyes off your core business. Focus on the good(s) and/or service(s) that resulted in your operation being in business in the first place. Your team has a core competency that requires time, resources, and a sharp focus. Don’t let a competitor jump ahead because you “missed a trick” thanks to key personnel wrangling with a protracted WMS upgrade.
- An IT Engineer isn’t exactly the same as a WMS Engineer. Just because your company has a team of technical folks who know SQL and Java, doesn’t mean they understand the full technical and functional scope of a WMS implementation, and this includes impacts on other systems like order management and labor management systems. An experienced WMS Engineer, whether installing a mini-hotfix or part of a team conducting a tier-1 WMS implementation with all new hardware, adds immense value to a WMS project versus a “generic technical person” with no WMS experience. An expert is paid for their expertise for a reason.
- It’s often cheaper to outsource when everything is taken into account. The correct calculation isn’t simply “savings equals “X” amount of money we didn’t pay another company by doing things ourselves”. The calculation should include the salaries of the people in-house who were away from their day job for lengthy periods of time. What’s harder to calculate is time loss due to task-switching, value that could have been added if your personnel were focusing on core business, and – even potentially greater – the cost that new defects or non-streamlined processes introduced by your in-house team that aren’t specialists. Here is another potential cost: Missed features that would be recommended and implemented by experienced supply chain execution professionals.
- Using full-time staff, whether existing or onboarded for the project, and existing company resources are both risky moves. Unlike when work is contracted outside to a trusted solution provider, one or more in-house staff leaving will certainly negatively affect your project timelines. Using/hijacking resources earmarked for your core business is also a risky proposition.
Real-World Example:
A 3PL decided to apply a small WMS hotfix directly to their production environment while simultaneously upgrading their mobile scanners from ancient terminal models. The “patch team” applied the hotfix and warehouse personnel immediately began experiencing crashes. They had to go back-and-forth with their vendor to find out that the hotfix is for a slightly newer WMS version. The mobile upgrade team successfully tested the new scanners with a test environment, but when they put them into production the entire network – and every application leveraging it – slowed to a crawl. It turns out that the mobile scanners were pushing more information, more quickly than the old legacy scanners and the network couldn’t handle it.
Both teams wasted time that could have been spent on more productive core business endeavors. The warehouse went down just briefly for the hotfix, but for much longer during the botched scanner upgrade as the problem was troubleshot. Personnel eventually had to resurrect the old terminals until the network infrastructure (and in-turn bandwidth) could be improved.
WMS professionals would have validated the proper WMS version, applied the hotfix in a test environment, and then applied it to production after testing. Drawing on previous experience with scanner upgrades, they would have also understood the “big picture” ripple effects and advised that the network infrastructure be upgraded appropriately.
Please note that none of the above suggests handing a hefty check to a solution provider and not paying attention. There should be at least a few folks within your organization with a functional understanding (technical-side is a bonus) of what needs to be done that work closely with your vendor to provide them with anything they need like systems access, data, etc…while prodding them to keep the schedule on-track.
Carefully select a solution provider based on your supply chain execution needs, and then build an ongoing relationship with them so that they become familiar with your systems and processes. Do you have any supply chain execution system challenges? Drop us a line, as this is our specialty.
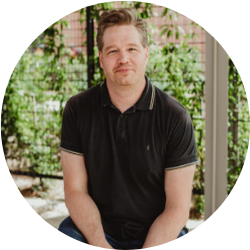
Written By James Prior
With over two decades in software pre-sales and implementation since 2000, James specialized in working with pre-sales teams and contributed to blog posts. For further information, please email sales@tryonsolutions.com.
More From This Category
Digital Transformation: The Key to Meeting Customer Expectations
In today’s fast-paced retail environment, customers expect seamless experiences whether shopping...
When to Hire a WMS Consultant
Your Warehouse Management System (WMS) is at the core of your supply chain operations. As the...
Industry 4.0 Solutions that are Transforming Warehouses
The warehouse industry is transforming with Industry 4.0 technologies, shifting from traditional...