TRYON BLOG
6 Tips to Properly Maintain Your Warehouse Management System

Your operation has successfully implemented a warehouse management system. Congratulations, as not all WMS implementations are successful – or so we hear, at Tryon Solutions we don’t have firsthand experience with that. Your next step post-implementation is ensuring that your team maximizes the value of your WMS and keeps it running smoothly. WMSes are powerful, oft-updated systems with their data and integration tentacles extending throughout your business, and this level of power and scale means that you can’t simply implement-and-forget and still get the most out of your system. In this article we’ll look at the top 6 tips to keep your WMS well maintained.
- Stay updated to enjoy the latest features and maximize efficiency, security, and integration. Systems are updated for a reason, whether to improve performance, fix an issue, or add a new feature. Older versions can also be expensive and trickier to support. If you aren’t on a continuous upgrade schedule, then at the very least your IT department should stay on top of the latest WMS versions and what they can potentially bring to the table.
- Conduct regular cycle counts and “data audits” checking that information all systems surrounding your WMS are in agreement. You absolutely MUST cycle count on a regular basis, and consider automatic cycle counts for popular and/or pricier items as they are deserving of the extra attention. Inventory accuracy percentage (Physical Count / Record Count X 100) is an easy-to-calculate, handy KPI to check inventory that is actually on the floor versus what’s counted in the WMS. Your WMS should also have some version of a “count variance” report.
- Check in with both warehouse personnel and any available user communities for advice on process improvements and dealing with common issues. Regularly meet with team leaders to find out what are the common concerns affecting personnel on the warehouse floor, as these in-turn will affect the performance of your WMS. A WLM (Warehouse Labor Management) system can also help get to the bottom of process flow issues.
- Keep your warehouse personnel sharp via regular training sessions and the related documentation up-to-date. All floor staff, WMS users non-users alike, should be trained and occasionally refreshed on best-practice process-flows. Make a point to check-in before peak season hits to see if anyone needs training (or retraining) on any of the key processes in your warehouse.
- Monitor the performance of your warehouse by regularly reviewing WMS and WLM (if you have one) dashboards. Check-in with location error reports and shipping dashboards in your WMS, the latter can enlighten on any shipping issues such as short loads, un-shippable or problem inventory (maybe due to holds or damage), and staging related issues. Any metrics on getting orders out on-time should take priority, as fulfilling service level-agreements with customers is why your operation is in business. Setup alerts that monitor select KPIs like order fulfillment rate (Orders Shipped / Orders Placed X 100). A key WLM analytic to review is employee (aka user) percent performance per task. and be sure to investigate the stats before making any declarations on performance as there could be extenuating circumstances for below standard numbers.
- Ditch the dinged-up scanner and stay on top of the latest warehouse technology, and especially anything that improves the flow of common bottleneck areas like receiving and order picking. Your team should keep an ear to the ground on the latest automation and other tech that would work well with your processes and systems that can drastically improve operations. For example, if you find your order picking is particularly pokey then look into cutting edge technologies like Locus Bots or perhaps a pick-to-light system. Your top competitors are getting rid of their legacy equipment to more quickly and cheaply serve their customers, are you?
Ideal World Example: Staying on Top of the Latest Tech
Warehouse managers caught wind of a new 2D bar-code scanner that is smaller, easier-to-use, and allows for faster scans. Their WMS needed an update to fully support it, which was handled before the new devices arrived. Post implementation and after a few brief training sessions with the new scanner, order picking was increased by 25 units per hour.
Horror Story: Neglecting User Training
An already bustling warehouse heading into a busy season brought a handful of new employees onboard, and management assumed they would learn best-practices by briefly shadowing veteran employees and then via their daily SOP. It was later uncovered that new staff were often storing inventory at their discretion during the putaway process, rather than going along with the more optimal system direction. Peak season arrived and warehouse personnel were hurriedly scrambling trying to fulfill orders with inventory that had been sloppily stored. Warehouse managers realized they should have set aside at least some time to properly train new hires rather than assuming they will learn strictly on the job.
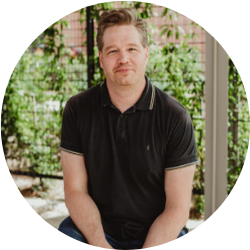
Written By James Prior
With over two decades in software pre-sales and implementation since 2000, James specialized in working with pre-sales teams and contributed to blog posts. For further information, please email sales@tryonsolutions.com.
More From This Category
Digital Transformation: The Key to Meeting Customer Expectations
In today’s fast-paced retail environment, customers expect seamless experiences whether shopping...
When to Hire a WMS Consultant
Your Warehouse Management System (WMS) is at the core of your supply chain operations. As the...
Industry 4.0 Solutions that are Transforming Warehouses
The warehouse industry is transforming with Industry 4.0 technologies, shifting from traditional...