How User Simulations Can Improve Warehouse Efficiency
We are always in the market for strategies and practices for improving warehouse efficiency, and making changes to a live warehouse is generally how we determine if they truly work. What if you could try them out and tinker without fear of negatively impacting operations? Simulating all warehouse activity over a work shift using production orders and receipts allows for the informed evaluation of warehouse process flows, layouts, and overall practices; it’s the ultimate readiness assessment.
One of our largest customers found more than a hundred issues through warehouse user simulations related to configuration and static data setup that would not have been discovered otherwise.
Warehouse user simulations allow you to…
- Benchmark operational metrics for all areas including inbound, inventory control, and outbound
- Validate application configurations for operations to meet or exceed service level agreements
- Reduce putaway and pick travel distance by optimizing the paths
- Optimize putaway and pick location slotting for SKUs
- Conduct management training by introducing different types of scenarios and real-world situations without disrupting the “live” WMS (digital twin)
- Validate operational reporting required for the management team to make labor decisions
- Save time and money via cost avoidance when major issues or defects are uncovered in the simulation
Let’s take a high-level look at how to do this:
- We need to mimic the warehouse in full operation, and that includes every user that logs in via terminal, like pickers, loaders, receivers, etc…We’ll use the group test functionality in our low-code performance testing solution of choice to accomplish this. The wave planners and shipping clerks can either be automated or human.
- Next we poll the labor management system for how long it takes to perform each operation, as any test automation solution worth its salt can simulate all users within warehouse(s) by using WLM engineering standards to delay each physical step within the warehouse as accurately as possible.
- All Inbound and outbound orders should be loaded into the system maintaining the same sequence and timing as the real world, and these are acted upon by the simulated users in our test solution.
- After running the simulation, check the LMS for travel and idle time, and total overall labor spent. Run the simulation again, but this time change inventory, slotting location, and/or workforce allocation, and evaluate the result on your “test model” AKA digital twin instance. You should feel free to continually change any configuration and/or data, and then run the simulation and check the results. The goal here is not necessarily looking for bugs, mainly we are validating configuration and resource allocation, and uncovering bottlenecks – and so we are optimizing the operational aspect moreso than finding software defects.
Can we make major tweaks directly to the real warehouse without testing them out on the digital twin? Sure, but it comes with risks. Performing a simulation on the twin prior to an upgrade or a new deployment drastically reduces risk, as you can expose management, application, and/or server based concerns before the go live.
These days warehouses and distribution centers are experiencing labor shortages. What is the impact if we run with less users/workers? How much is it worth to you to optimize your workforce?
If you would like some help improving warehouse efficiency via simulations, feel free to drop us a line.
This post was written by:
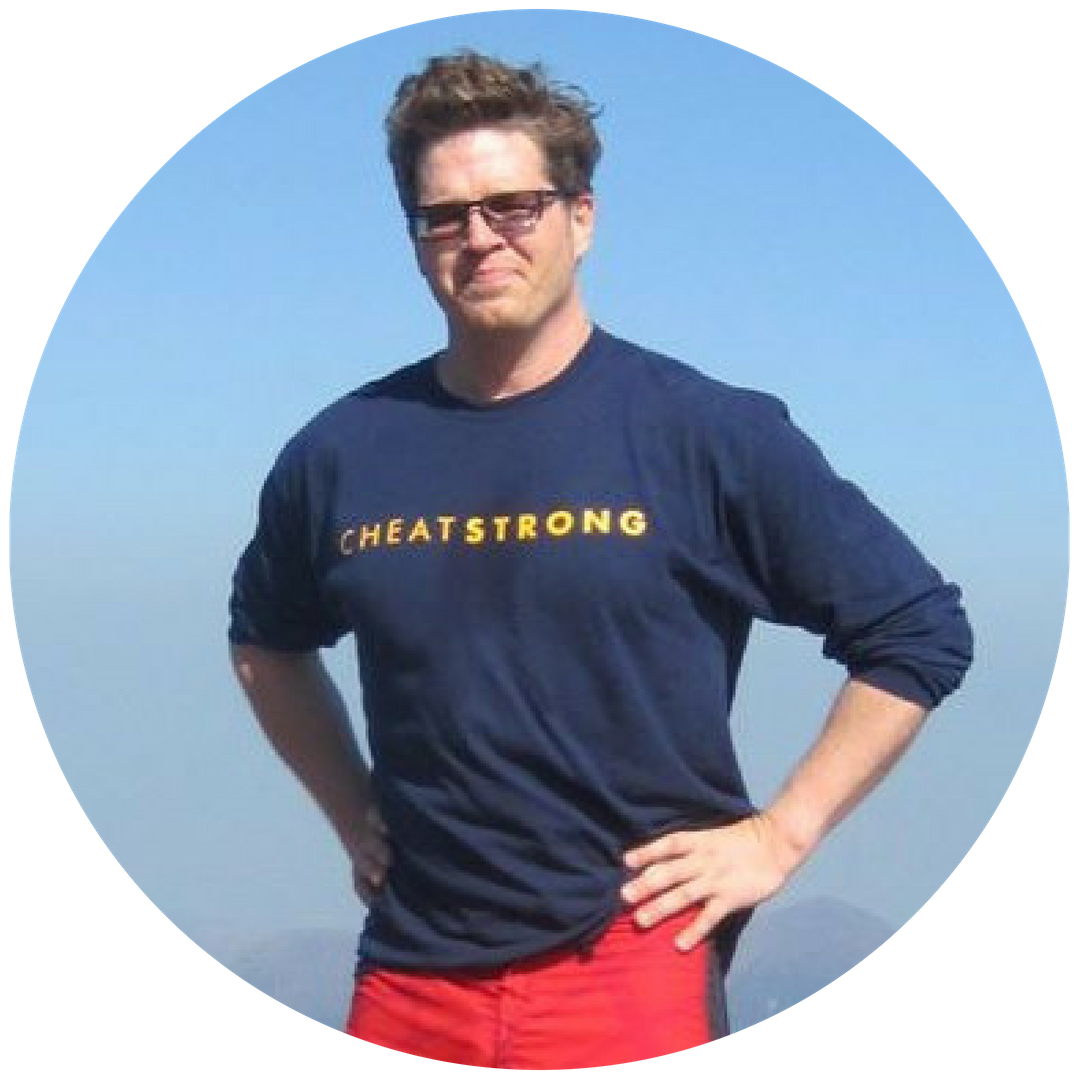
James Prior Sales Ops Manager James has been working in software pre-sales and implementation since 2000, and more recently settled into working with a pre-sales team and occasionally writing blog posts. Drop him a line at: james.prior[at]tryonsolutions[dot]com.
Recommended Content
SLA Optimization Worksheet
Enhance your service level agreements (SLAs) with this SLA Optimization Worksheet. Use it to assess your current systems, identify gaps, and create a roadmap for improvement. Includes actionable steps, KPIs, and next steps to boost efficiency and customer satisfaction.
Optimizing Layer Picking Efficiency for Large Global Company
A large global company optimized its automated layer picker, reducing manual layer picking by 70% through seamless integration with Blue Yonder WMS and Robotics Hub. Tryon Solutions developed API endpoints, real-time reporting, and a pick face manager to enhance...
Digital Transformation: The Key to Meeting Customer Expectations
In today’s fast-paced retail environment, customers expect seamless experiences whether shopping online or in-store. Shipped-to-home orders, in-store pickups, and last-minute changes are now the norm. However, many businesses struggle to meet these demands due to...
Tryon Solutions for Test Management
At Tryon Solutions, we design tailored Test Management strategies that help you proactively identify failures and streamline testing processes. Our expertise ensures your systems are reliable, safeguarding your operations from costly downtime. Download the brochure...
When to Hire a WMS Consultant
Your Warehouse Management System (WMS) is at the core of your supply chain operations. As the demands on your warehouse evolve, ensuring your WMS is future-proof is critical to maintaining efficiency, meeting customer expectations, and staying competitive. But when is...