How to Calculate Warehouse Management System ROI
We should all know by now that a WMS is worth it for medium-to-humongous warehouses and distribution centers versus a pen-and-paper system. With that said, just how “worth it” is the investment in WMS? In which specific areas are we reaping the most benefits, and what’s our return-on-investment scorecard for each? More focused and less complex systems usually come with a handy dashboard that displays direct ROI. You can simply show the boss, he/she slaps you on the back, your team declares victory, and you all go out for a celebratory ale or lager – or instead perhaps for those hoppy, funny-name craft beers with the hand drawn labels that everyone pretends to like.
Now in the WMS world, there so many varied and complex areas of an operation in play that we need look deeper. Some of the benefits are tangible and others, while equally important and obvious, are harder to finely measure. In this article we’ll provide ideas to determine and understand WMS ROI, whether you are doing a cost-benefit analysis to decide if you should take the WMS plunge or if you are already sold and are preparing for a before-and-after study. What we’ll be discussing here also applies for studies and benchmarks in specific WMS areas.
We’ll need to calculate the total cost of ownership for our WMS, including cost of the license, training, implementation, any requisite hardware, downtime(s), and ongoing costs for consumables. Let’s set this total aside for the moment. It will be an intimidating figure at a glance, but let’s look at what we are getting for our money.
Mostly Quantifiable Benefits:
Let’s first tackle benefits that are relatively easily measured and confirmed, things like improved order accuracy, less fulfillment errors, and reduced handling costs.
We’ll be looking at both warehouse and clerical labor savings a lot in this article, but certainly one of the largest expenditures of labor is the need for multiple physical inventories or non-optimal cycle counting along with the inevitable manual inventory tracking/searching that result from these efforts. There is a drastically reduced necessity for this with a top tier WMS. Tally up the amount of labor hours spent performing these time-consuming counts and searches, and compare against the total after the implementation dust settles. The intangible benefit is what your personnel could be productively doing for your operation instead of rummaging around various warehouses on a boring “treasure hunt” for a missing case of hot pink fidget-spinners.
A certain percentage of those costly “hunts” are fruitless and the inventory is written off as lost, and there is of course an associated dollar value. With the increase in visibility and accuracy afforded by WMS, there will certainly be less write-offs and so your team should total the amount of lost inventory before WMS and weight it against the post-implementation numbers.
The increased visibility also allows for more accurate forecasting which means less need to carry excess inventory as well as less chance to run out of inventory, reduced likelihood of having to ship product from one location to another (after initial distribution), and a decreased possibility of inventory obsolescence (happens often with tech items). You used to ask your “replen guru” in the warehouse how many turbo-widgets are needed for future orders, and they would stare at the ceiling for a while and then proclaim “four-hundred and thirty-seven!” WMS provides drastically improved visibility that swaps “gurus” for more accurate dashboards. So, let’s add up the cost of inventory obsolescence, the total amounts for having to ship products from one location to another, and if we know the labor involved let’s include that in as well and we’ll compare these numbers post-WMS implementation. What is trickier to exactly tally are all the additional logistical movements associated with handling extra inventory in the warehouse, and lost sales opportunities from not having adequate stock.
Blue Yonder’s Luminate offers predictive capabilities in the supply chain planning arena. It helps with situations where one location usually sells X number of turbo-widgets, and another location often sells Y number of turbo-widgets, and so a prediction is made based on historical demand for a particular location in a particular timeframe. You want that turbo-widget on the right shelf for the customer at the right time.
With the overall efficiency and speed improvements coupled with the required customer data flowing through the WMS to printed labels, there should be less compliance fines post-implementation. This figure should be easily calculated and compared.
This is underrated; be sure to keep track of any new business opportunities resulting from capabilities and/or capacities introduced by your WMS. For example, a potential customer requiring API or EDI data can now do business with your operation.
We can also look at clerical labor savings for all manual data entry and the resulting errors its more likely to introduce, as there is more automation and less key-punching with a warehouse management system. Be sure to put the sum total of pre-WMS keypunch hours against your post-WMS numbers, as it’s nice and clean easy-to-showcase ROI. Your team should before-and-after track common key performance indicators (KPI), like total re-work, re-stock, cycle re-counts, mis-picks, order fulfillment errors, order throughput, and overtime orders. Every operation is unique, and so certainly if you have your own KPIs then you should compare those as well.
Harder-to-quantify / Intangible Benefits:
The huge inventory management and logistics improvements allow for managers to focus on process optimizing along with the timely, organized and insightful data and reporting which allows for better decision making, and more time for things like adding new business opportunities.
Employee moral may be boosted as managing the warehouse will be easier and a bit less stressful; look for this well after the kinks are ironed out and employees are used to the new system. In a related bonus, stress balls should see less wear-and-tear.
Faster, more accurate order processing and stricter adherence to compliance rules all ultimately mean better customer service and stronger industry reputation.
When showing off the numbers for your WMS justification to the boss, be sure to mention the intangibles listed above as well. While it may be harder to attach precise numbers, an executive can still understand if your operation will reap the benefits and should have a ballpark figure in mind. Using a WMS also opens up avenues for further ROI over time, as it nicely integrates with big ROI generators like Transportation Management Systems (TMS) and Warehouse Labor Management Systems (WLM).
Could you use some assistance calculating WMS ROI? Whether debating taking the WMS plunge or maybe you want to prove the value your existing system, either way drop us a line and we’ll help out!
This post was written by:
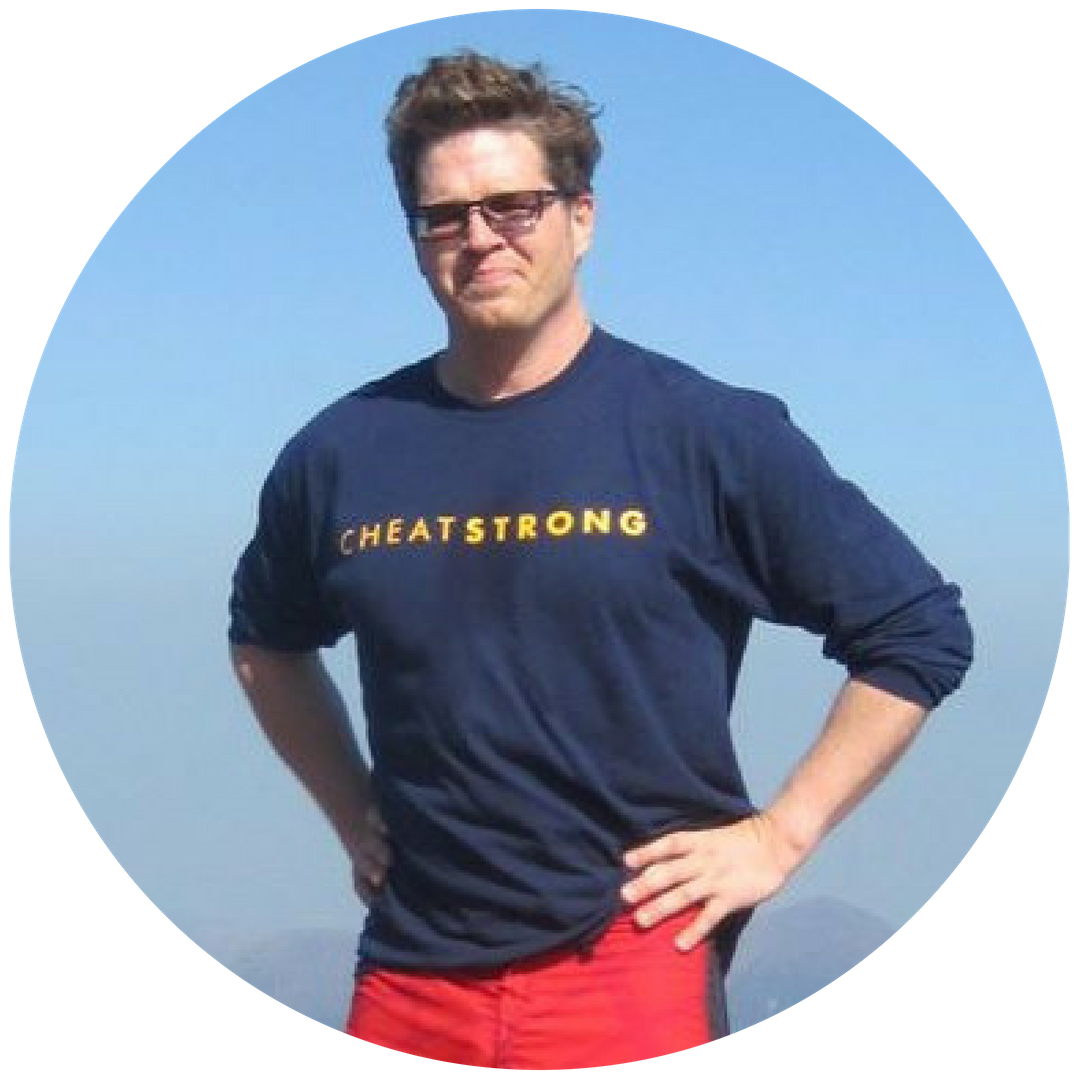
James Prior Sales Ops Manager James has been working in software pre-sales and implementation since 2000, and more recently settled into working with a pre-sales team and occasionally writing blog posts. Drop him a line at: james.prior[at]tryonsolutions[dot]com.
Recommended Content
6 Levers for Smarter WMS Support
Whether you're juggling school drop-offs, remembering a birthday party, or trying to reply to that one group text before dinner hits the table, modern life pulls us in a hundred directions at once. That constant pressure to keep up, stay flexible, and deliver—no...
WMS Lift-and-Shift the Top 10 Reasons to Move from On-Prem to SaaS
Over the last couple of years there has been a major push on all enterprise systems to move to the cloud. This includes ERP, CRM, HRIS, PLM, SCM, BI, MES, etc. The acronyms could go on forever. Each organization has their reasons for the move, but most fit into three...
5 Signs Your Software May Not Be FSMA Rule 204-Compliant
Is your current software keeping up with the new requirements of FSMA Rule 204? If you're not sure, you're not alone. Many companies are discovering their systems aren't quite ready for the level of traceability, visibility, and data accuracy now required. Here are...