TRYON BLOG
Beat the Competition on Order Fulfillment Accuracy and Speed in 2024

The demands behind customer order fulfillment speed and accuracy ultimately drives nearly everything that happens in a warehouse. Customer expectations continue to increase in 2024, with no signs of abating in the coming years.
Streamlining processes and logistical movements always helps but really, it’s the march of technology in the supply chain that allows for you to get your XL hissing cockroach terrarium (no judgement, you like what you like) delivered the same day that you think to place the order. You also want to watch as the delivery process unfolds in real-time, and then be able to quickly return the terrarium once you realize that it should have been an XXXL. These expectations are met via inordinate amounts of time and money on the supply chain side. Not only that, we now have peaks like Black Friday, Prime Day, and other sales events that often bust the order management seams in our warehouses and distribution centers. Your top competitors are keeping up, so what should you do?
Find Out Where Things Stand:
This might seem obvious, but be sure to check-in both with your customers AND your order pickers to see if they have any concerns that need addressing. Your team should also review any related WMS dashboards AND be sure to calculate Order Fulfillment Rate:
Order Fulfillment Rate is the percentage of orders shipped to customers from current inventory without lost sales or the need for backordering. This is a key statistic to monitor, as it covers a variety of more specific order related metrics in one and accurately reflects your operation’s ability to meet customer demand. You can also use it to help plan procurement for future orders. The calculation is: Total orders shipped / Total orders placed x 100
Aim high for your team’s OFR, shoot for 98 percent or even higher.
What We Can Do:
Take it back to the basics and ensure that your team is strategically locating inventory in the right place. Order picking will suffer if you are not putting some thought into slotting and/or performing the putway process properly. Your team should also ensure that inventory data is correct by conducting regular cycle counts, and of course verify that all processes picking depend on (basically everything) are as streamlined and efficient as possible.
Going beyond the basics, what about your picking strategy? Choosing the correct one depends on a variety of factors including order sizes, warehouse layouts/configurations and business needs. By taking into consideration the advantages, disadvantages and best practices for each option, your organization can ensure its picking system meets the demands of your orders. For example, discrete order picking tends to be a more consistent method of pulling inventory but the increased accuracy may not be worth the extra time it takes.
No single investment can increase units picked per hour and decrease error rates like robot pickers. Our engineers have witnessed firsthand the before-and-after improvements at several clients and the bots not only speed up what they handle, but they also make human pickers more efficient because they are less worn out. There is of course a sizeable initial capital investment, but the ROI is even more sizeable after the dust settles. When debating which robot pickers to implement, and there is no shortage of options here, be sure to check for case studies highlighting ROI for operations similar to yours.
Maybe your operation isn’t quite ready for full-on automation, but we both know you can’t afford to outright disregard technology. Ditch the old tech, but also consider the hardware and software components in-and-around order picking where a better mousetrap has been built. Evaluate things like improved pick-to-light solutions, voice or vision picking, faster bar-code scanners, and better bar-codes. Take the latter option for example, the numbers behind bar-codes that are damaged to the point of being rendered unreadable must be human entered and this slows everything down while potentially introducing errors.
If picking at your warehouse is especially labor intensive and automation isn’t an option, then your team should evaluate a Warehouse Labor Management (WLM) system. Labor can be measured, managed, and planned just like anything else. A properly implemented WLM helps with coaching personnel, work schedule optimization, establishing labor standards, and allows for increased workforce visibility. It will optimize everything of course, but a WLM could additionally be used to diagnose and resolve any labor related issues in your pick process flows. A WLM can provide insight if a picker is taking an inordinate amount of time to complete their assigned tasks; perhaps the root cause is that they are doing extra work due to a faulty bar-code scanner or maybe it’s something even simpler like the picker is cleaning work areas while picking.
Could it be that your order management or warehouse management systems are a hinderance? The ability to quickly push out orders will certainly be negatively impacted if your OMS and/or WMS can’t scale with growth or keep up with intricate customer compliance requirements. The requirements behind millions of inventory movements shipping out to a large group of customers are serious, and this requires equally serious tier-1 (or at least tier-2) systems.
AI systems will be handling order picking in the future. They can analyze the warehouse layout and use cameras to instantly locate items, and then determine the most optimal order for picking to minimize travel time. Cameras can additionally be used to verify that the correct items are picked. AI can also use historical data to predict which items are more likely to be ordered together and which are more likely to be ordered at a certain time, and with this intel more popular items can be located closer to pick areas. Pair this intelligence up with robots and it’s clear that at some point in the foreseeable future humans will strictly be monitoring picking and not performing it.
We know AI driven robots will take over order picking duties at some point, but in the right here-and-now are your competitors delivering value faster to your top customers? If your team needs help increasing customer order accuracy and/or speed, then please feel free to drop us a line as this is what we do regularly for our clients.
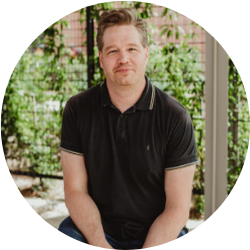
Written By James Prior
With over two decades in software pre-sales and implementation since 2000, James specialized in working with pre-sales teams and contributed to blog posts. For further information, please email sales@tryonsolutions.com.
More From This Category
5 Supply Chain Systems Enhancements for Consumer Goods
Line up! The battle for the top systems enhancements for consumer packaged goods (CPG) companies...
4 Compelling Reasons to Outsource Supply Chain Execution Services
Why would one outsource when it’s technically possible to handle everything in-house? I’m a fan...
5 Ways to Uncomplicate the 3PL Industry
The Known: All modern 3PL (third party logistics) operators should offer a comprehensive range of...