TRYON BLOG
Industry 4.0 Solutions that are Transforming Warehouses

The warehouse industry is transforming with Industry 4.0 technologies, shifting from traditional methods to innovative solutions that enhance efficiency, reduce costs, and improve productivity. These advancements go beyond automation, making warehouses smarter, more agile, and more connected.
We know Industry 4.0 solutions can be overwhelming, but we’re here to organize the information and make it easy to explore how these technologies can enhance your operations. In this interactive blog, we’ll guide you through the top Industry 4.0 solutions revolutionizing warehouse operations. Simply click on the “+” to the left of each solution to learn even more about its key applications. Embracing these innovations will make your warehouse smarter, more efficient, and more connected, giving you a competitive edge in today’s rapidly evolving supply chain.
1. Artificial Intelligence (AI) and Machine Learning
AI is one of the most transformative technologies in modern warehousing. It provides intelligent automation that extends well beyond basic robotic functions, offering predictive capabilities, data-driven insights, and decision-making that can optimize warehouse operations in real-time.
Key Applications:
AI-Driven Demand Forecasting
AI and machine learning algorithms analyze historical data, sales trends, and external factors to forecast demand more accurately. By predicting future inventory requirements, warehouses can optimize stock levels, reduce overstocking, and avoid stockouts, resulting in improved inventory management and cost savings.
Automated Decision-Making
AI systems can evaluate multiple data points simultaneously to make real-time decisions about inventory management, order routing, or scheduling. For instance, AI can decide which orders to prioritize or which products need to be restocked based on predictive analytics, minimizing delays and improving throughput.
Intelligent Analytics
AI-driven analytics provide insights into warehouse operations that were previously difficult to obtain. These insights help optimize processes such as warehouse layout design, picking routes, labor allocation, and more. By leveraging AI to analyze large sets of data, warehouses can improve efficiency, reduce operational costs, and enhance service levels.
2. Robotics
Robotics are perhaps the most visible manifestation of Industry 4.0 in warehousing. From mobile robots to robotic arms, these machines are becoming indispensable in the warehouse, performing tasks that once required human intervention, and doing so with speed and accuracy.
Key Applications:
Automated Guided Vehicles (AGVs)
Automated Guided Vehicles are mobile robots that transport goods throughout the warehouse, eliminating the need for human operators to drive forklifts or other material handling equipment. AGVs help improve warehouse efficiency by optimizing traffic flow, reducing the likelihood of human error, and allowing employees to focus on more complex tasks.
Robotic Picking and Packing
Robotic arms and automated systems are increasingly being used to pick items from shelves and pack them into boxes for shipment. These robots use advanced vision systems and machine learning to identify and handle products, reducing human error, speeding up the picking process, and improving overall accuracy.
Collaborative Robots (Cobots)
Cobots work alongside human operators to assist with tasks like picking, sorting, and packing. These robots are designed to be safe and intuitive, allowing human workers to focus on more complex tasks while robots handle the repetitive work. Cobots are particularly useful in high-demand environments where human operators might otherwise struggle to keep up.
3. Internet of Things (IoT)
IoT technology is playing a pivotal role in the warehouse of the future, enabling the connectivity of devices, sensors, and systems to create a more transparent and responsive environment. By integrating IoT into warehousing operations, businesses gain better visibility into inventory levels, asset conditions, and equipment health.
Key Applications:
Real-Time Tracking and Monitoring
IoT sensors are used to track assets and inventory in real-time, providing up-to-the-minute information about stock levels, product conditions (temperature, humidity), and location. This real-time data enables better decision-making, reduces the risk of stockouts, and allows for faster response times to supply chain disruptions.
Smart Shelves and RFID
RFID tags and smart shelves allow for automatic tracking of products as they are added or removed. This technology minimizes the need for manual stocktaking, increases inventory accuracy, and allows for a more efficient and streamlined approach to stock management.
Predictive Maintenance
IoT-enabled devices are used to monitor the health of equipment such as forklifts, conveyor belts, and other machinery. By analyzing data from sensors, predictive maintenance systems can identify potential issues before they become problems, allowing warehouses to take preventive action and avoid costly downtime.
4. Warehouse Management Systems with Advanced Features
A modern Warehouse Management System (WMS) is the backbone of any Industry 4.0 warehouse. Today’s WMS have evolved beyond simple inventory tracking and order management, incorporating advanced technologies like AI, machine learning, and cloud computing.
Key Applications:
Cloud-Based WMS
Cloud-based WMS platforms offer a flexible and scalable solution for warehouse management. They provide real-time access to inventory data, enable remote monitoring, and seamlessly integrate with other enterprise systems such as ERP (Enterprise Resource Planning) and TMS (Transportation Management Systems). This integration improves visibility, coordination, and accuracy across the entire supply chain.
Voice-Activated Picking
Voice-directed picking systems are another example of how WMS has evolved. Using wearable devices like headsets and microphones, workers can receive instructions via voice commands, helping them navigate the warehouse more efficiently and reducing errors. This hands-free solution improves productivity and allows workers to focus on tasks without being distracted by manual data entry or checking paper orders.
Mobile Solutions
Mobile solutions enable warehouse staff to use handheld devices to access WMS functionality directly from the warehouse floor. These devices allow workers to update inventory records, locate items, and track shipments in real time, enhancing overall operational efficiency.
5. Automated Sorting Systems
Sorting is a critical process in the warehouse, especially when handling large volumes of orders. Automated sorting systems are designed to quickly and accurately classify products, improving throughput and reducing the need for manual intervention.
Key Applications:
Conveyor Systems
Automated conveyor systems move products from one location to another, often equipped with sortation features that automatically direct items to the correct location based on predefined criteria. Conveyor systems save time and effort, streamline the sorting process, and reduce bottlenecks during peak periods.
Smart Sorting
AI-powered sorting systems use real-time data to optimize sorting routes based on factors like order priority, product dimensions, and shipping destination. These systems help warehouses maximize efficiency and ensure that products are dispatched on time.
6. Digital Twins
A digital twin is a virtual replica of a physical warehouse, providing a digital model that mirrors the real-world environment. Using data from IoT devices and sensors, digital twins simulate warehouse operations, allowing businesses to test changes and optimize processes before implementing them in the physical space.
Key Applications:
Simulating Warehouse Operations
Digital twins allow warehouse managers to simulate different scenarios (e.g., changing product layout, altering picking routes) to determine the best approach for maximizing efficiency. This risk-free testing environment enables warehouses to make data-driven decisions with greater confidence.
7. Drones and Autonomous Vehicles
Drones and autonomous vehicles are no longer science fiction—they are actively being used in warehouses to improve inventory management, order picking, and delivery.
Key Applications:
Inventory Management Drones
Drones equipped with barcode scanners or RFID readers can fly through the warehouse to conduct automated inventory counts. These drones improve stock accuracy and reduce the time spent on manual stocktaking.
Autonomous Mobile Robots (AMRs)
AMRs are used to transport goods within the warehouse, automatically navigating through aisles, picking up and dropping off items as needed. These robots are designed to work autonomously without the need for human supervision, reducing labor costs and increasing operational efficiency.
8. Augmented Reality (AR)
Augmented Reality (AR) is revolutionizing warehouse operations, especially in areas like picking and training.
Key Applications:
AR Glasses for Picking
Warehouse workers can wear AR glasses that overlay real-time information about products, including their location, quantity, and order number. This enhances picking speed, reduces errors, and provides workers with an intuitive way to interact with the WMS system.
AR for Training
AR can also be used for employee training, offering hands-on experiences that simulate warehouse tasks in a controlled, interactive environment. This type of training helps workers get up to speed faster and reduces the likelihood of costly errors during the learning process.
9. Blockchain for Transparency and Security
Blockchain technology provides a secure and transparent way to track goods as they move through the supply chain, including warehouse operations.
Key Applications:
Traceability and Transparency
Blockchain creates an immutable ledger that records every transaction involving goods within the warehouse, from receiving to shipping. This system ensures that all stakeholders have access to accurate, real-time information about product movements, helping improve transparency and accountability.
Smart Contracts
Blockchain-enabled smart contracts automate processes such as inventory restocking or order fulfillment based on predefined conditions. These contracts execute automatically when specified conditions are met, improving efficiency and reducing administrative work.
10. Testing Software
With the integration of advanced technologies ensuring that all systems function seamlessly is essential to maintaining efficient and reliable operations, even minor software glitches can cause significant disruptions.
Key Applications:
Automated Testing for WMS
Warehouse Management Systems are at the heart of any Industry 4.0 transformation. These systems must be thoroughly tested to ensure they work correctly in a dynamic, high-volume environment. Automated testing for WMS allows warehouses to test system updates, integrations, and new features faster and more accurately. By simulating real-world scenarios, automated testing can identify potential issues before they impact operations.
End-to-End Supply Chain Testing
The interconnected nature of modern supply chains requires end-to-end testing to ensure all systems work together without disruption. Whether it’s inventory management, order fulfillment, or transportation management, testing software solutions across the entire supply chain helps ensure that every part of the process is running smoothly and that delays or errors are minimized.
Performance and Scalability Testing
As supply chains grow and evolve, systems need to handle increasing loads without compromising performance. Performance and scalability testing assess the ability of warehouse systems, like WMS and IoT networks, to function under high-demand conditions. This type of testing ensures that the system can scale as needed to meet growing inventory and operational demands.
Continuous Testing for Continuous Improvement
Industry 4.0 technologies are continuously evolving, meaning software must be updated regularly to keep pace with new features and capabilities. Continuous testing allows warehouses to monitor their software solutions on an ongoing basis, ensuring that new functionalities are properly integrated, and performance remains optimized.
Industry 4.0 is not just a buzzword—it is a transformative force in the world of warehousing. By adopting technologies such as AI, robotics, IoT, and blockchain, warehouses are becoming smarter, more efficient, and more agile than ever before. As these technologies continue to evolve, warehouses that embrace them will be better equipped to meet the demands of an increasingly complex and fast-paced supply chain environment.
If your warehouse isn’t leveraging Industry 4.0 solutions yet, now is the time to start. The future of warehousing is digital, and those who act now will reap the benefits of a more efficient, cost-effective, and future-proof operation.
Give us a call or send us an email, and we’ll help you identify the best technologies to optimize your operations!
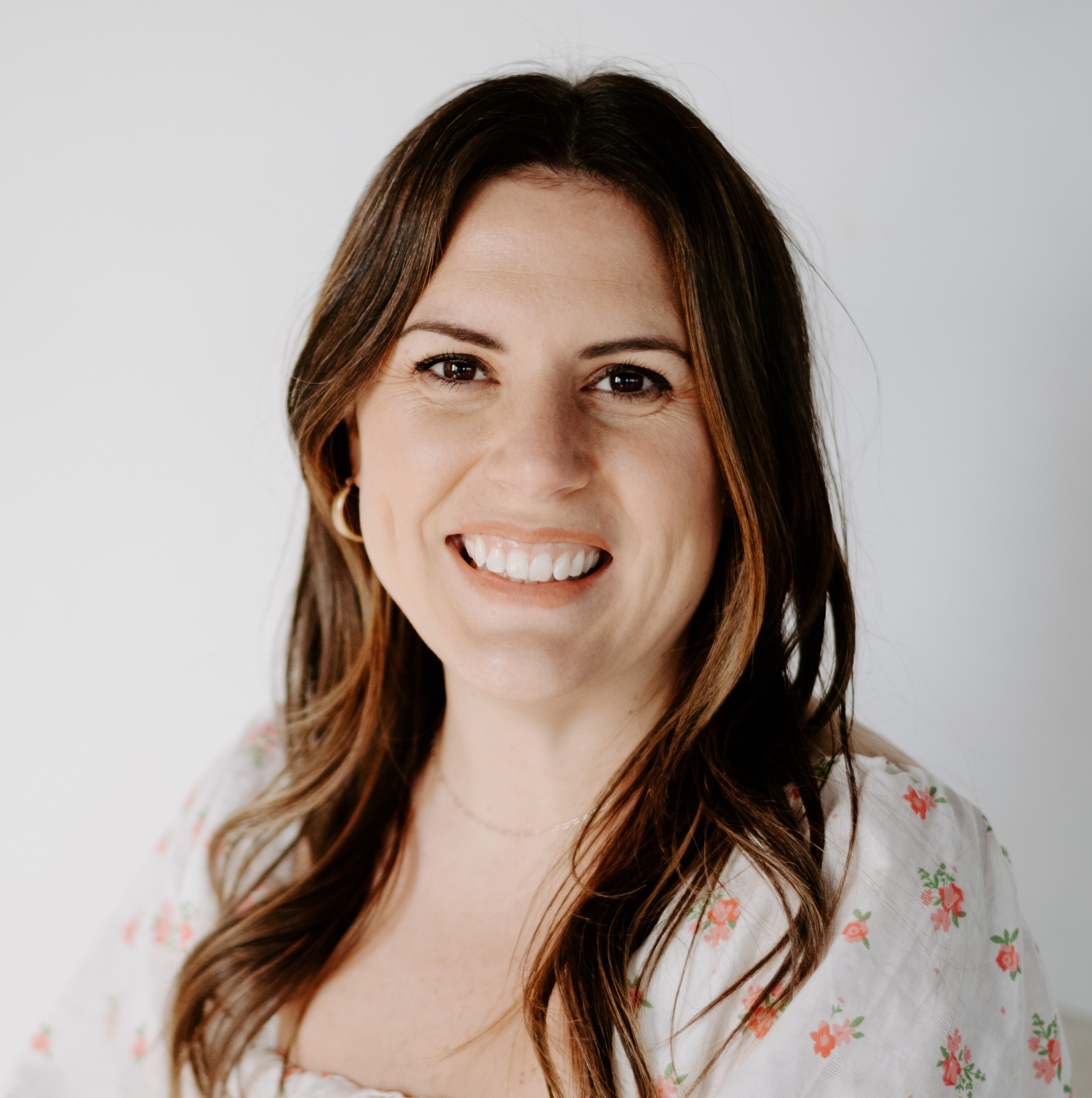
Written By Ashley Feldpausch
Ashley is a marketing professional, specializing in Warehouse Management Systems and leveraging strategic insights to drive growth, innovation, and customer engagement in the supply chain industry. For further information, please email sales@tryonsolutions.com.
More From This Category
6 Levers for Smarter WMS Support
Whether you're juggling school drop-offs, remembering a birthday party, or trying to reply to...
WMS Lift-and-Shift the Top 10 Reasons to Move from On-Prem to SaaS
Over the last couple of years there has been a major push on all enterprise systems to move to...
5 Signs Your Software May Not Be FSMA Rule 204-Compliant
Is your current software keeping up with the new requirements of FSMA Rule 204? If you're not...