Choosing the Right Technology for Your Picking Strategy
In Part I of our “Picking Strategy and Tech” series, I mentioned that Distribution Centers are going to have to deal with more diverse order profiles in this new digital age as wholesale orders are changing from Pallet size orders to case size orders. Digital orders from the web will be more frequent with smaller number of items, because the customer is only ordering what they need and picking processes will need to be modified accordingly. In this section, I am highlighting the possible picking technologies that will enable the new processes.
Picker to Item
Sending the picker to the items in the picking area is a traditional and the most common method of picking. The material storage fixtures in the pick area range from Rack Shelving, Pallet or Case Flow Rack, and Bin Shelving. To utilize the cube of the DC with high ceilings, Pick Modules and mezzanines are being used. To aid in picking the correct item and quantity for the order, technology has replaced the traditional pick list: RF Scanners, Pick-to-Light (pictured below) and Voice picking are the most popular technology to assist the picker. The relatively new Pick-by-Vision, which incorporates augmented reality tech to help pickers, is another option as well.
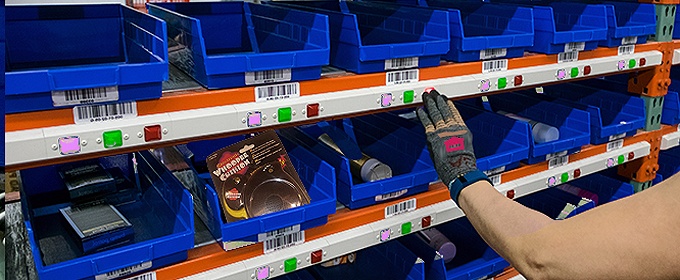
Pick-to-Light
The main advantages for sending the picker to the item are when labor and square footage of the DC costs are lower relative to using other technologies. Many pickers can be put into action to improve the throughput of the facility.
Item to Picker
More advance technologies are available that bring the item to the picker. These technologies include Carousels, Mini-Loads, Automated Storage & Retrieval and Mobile storage systems. Carousels are motorized bin shelving on rails that rotates the items stored on the shelving to a picking station. Carousels include both horizontal and vertical direction and are sequenced to coordinate multiple carousels to improve picking through put. Automatic Storage and Retrieval Systems (ASRS) are an integrated set of lifts that transverse through storage rack picking up containers and bringing them down to picking stations. The classic ASRS is for pallet storage and retrieval. When referring to case sizes or less than cases, Mini Loads are the technology used. Another type of ‘Item to Picker’ technology are Mobile storage units, like automated guided vehicles they roll the storage device to a picking station highlighting the position on the shelf to pick the product from.
In most cases, these ‘item to picker’ technologies are coordinated in such a way to keep items in front of the pickers to minimize picker wait time and to maximize their productivity. To achieve this, multiple sequenced pieces of technology are used, sometimes making the cost of the technology prohibitive for the productivity gains.
The main advantage for this type of technology to be deployed in DC’s is in areas where labor rates are higher and/or floor space is pricey enough to justify the expense. The throughput restrictions of the technology, typically means that these ‘item to picker’ technology will not work for higher volume items. Thus, the technology must be reviewed with the order profile to cost and through put justify the technology. For example, many smaller lower volume items can increase their storage density in a pick area when using an ‘item to picker’ technology. Amazon bought Kiva Systems’ mobile storage units to own the technology for their smaller lower volume items like books; now known as Amazon Robotics.
Put to Order Technology
As discussed in the previous article, Batch Pick Technologies have a solid foundation in Digital Distribution centers where Web Promotional items generate a spike of demand for a few items. These few items are waved together to generate a large quantity to be picked in bulk and sent to the ‘Put to Order’ technology to be divided up by order and combined with the other items of that order.
‘Put to Order’ technologies range from highly mechanized unit sorters to simple pallet/bin shelving (Put-Walls) to collect the multiple items being picked for an order. Often the technology will use a light system that directs the associate to the order location to put a specific number of items in the outbound shipper. For high volume facilities, a unit sorter (pictured below) which is typically a tilt-tray, Bombay or cross-belt type is used to marry up items from different pick zones across the facility.
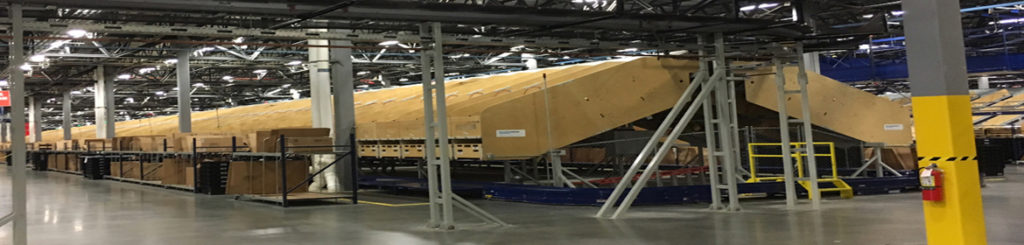
Unit Sorter
Medium volume facilities with many SKU’s which still have multiple pick zones, may use Put-Walls to combine the items from the multiple pick zones. Lower volume facilities may combine ‘Item to Picker’ technologies with Put-Walls to capture all the items of the order.
Storage Technology to Compliment Picking
Digital Distribution centers are laid out in a multitude of ways to aid the technology being used for picking. For ‘Picker to Item’ technologies, pick modules were mentioned as forward picking storage means to utilize the cube of the facility. Other type modules may be used, for high volume items Very Narrow Aisle (VNA) storage should be used in conjunction with throw lines to peel off cases and send them to ‘Put to Order’ technologies. For higher to middle volume items, a Pick Module know as a Shave Tower can be used to move pallets of product to the tower so they can be picked to a conveyor line.
To utilize the cube of the facility when ‘Put to Order’ technology is being used, mezzanines are used so both the upper and lower levels are being productive. Value added services and packing stations maybe positioned on one level while the ‘Put to Order’ technology is being used on the other level.
Robot or Cobot Technology
As discussed in the Zone Picking section, Cobots (Robots that move orders to people for them to pick the items to the orders) are finding their way into more Digital Distribution opportunities. Because a person does not have to travel with the orders up and down aisles to perform the picking and only walk between Cobots to perform the picks in a defined zone, through-put and productivity improves 2-3x.
Currently Co-bots that are finding their way into digital distribution opportunities have been tote or carton carrying robots. Pallet moving co-bots are making strides to become more prolific, as the smaller tote moving robots, are but they are limited by not being able to pass another robot in a standard 10’ aisle width and thus are limited to following pickers through a pick path, which defeats the purpose and eliminates the productivity gains of zone picking. Some manufacturers of pallet moving robots are improving their laser guidance systems and in the near future they will be able to pass in 10’ aisles and their use in distribution will soar.
Another type of Robot used in distribution has a robotic arm associated to an automatic guided frame and picks items from open containers to the tote or shipping container. The requirement on what can be picked by the robotic arm is restrictive and makes this an emerging technology.
Other Robots are being used in sortation applications and goods to person applications, making the use of robotics in distribution centers becoming more and more relevant.
Robotics Future in Distribution:
Distribution Industry Challenges:
|
![]() |
Robotic Technology Response:
|
Robotic adoption rate will increase 2x over the next 5 years. Extending to 70%+ of firms. (Source: MHI 2021, Annual Industry Report)
If you are in the market for a robot picker, we highly recommend Locus Robotics as they have done fantastically by our clients. Drop us a line, and we’ll chat – and while we like robots, we don’t fancy chatbots – about the increase in ROI we’ve seen at our customer sites.
This post was written by:
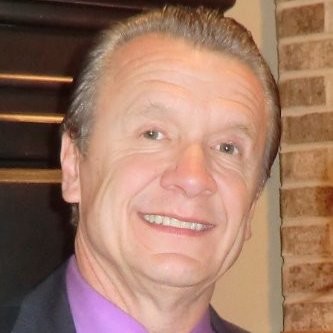
Recommended Content
SLA Optimization Worksheet
Enhance your service level agreements (SLAs) with this SLA Optimization Worksheet. Use it to assess your current systems, identify gaps, and create a roadmap for improvement. Includes actionable steps, KPIs, and next steps to boost efficiency and customer satisfaction.
Optimizing Layer Picking Efficiency for Large Global Company
A large global company optimized its automated layer picker, reducing manual layer picking by 70% through seamless integration with Blue Yonder WMS and Robotics Hub. Tryon Solutions developed API endpoints, real-time reporting, and a pick face manager to enhance...
Digital Transformation: The Key to Meeting Customer Expectations
In today’s fast-paced retail environment, customers expect seamless experiences whether shopping online or in-store. Shipped-to-home orders, in-store pickups, and last-minute changes are now the norm. However, many businesses struggle to meet these demands due to...
Tryon Solutions for Test Management
At Tryon Solutions, we design tailored Test Management strategies that help you proactively identify failures and streamline testing processes. Our expertise ensures your systems are reliable, safeguarding your operations from costly downtime. Download the brochure...
When to Hire a WMS Consultant
Your Warehouse Management System (WMS) is at the core of your supply chain operations. As the demands on your warehouse evolve, ensuring your WMS is future-proof is critical to maintaining efficiency, meeting customer expectations, and staying competitive. But when is...