Go Live Checklist for WMS
Every implementation needs a Go Live Checklist for WMS so your team can systematically ensure that no critical steps were overlooked in the leadup to a major deployment. Below is a handy top-down, overall go live checklist for wms that we left blank so you can cut-and-paste, make a handful of tweaks specific to your project, and GO. You might also need an additional “customer expectations” or “deliverables” checklist depending on the scale of the project and your customer agreement(s). Please consider this a companion piece to our equally helpful Go Live Nuggets of Wisdom article.
Assignments and User Roles |
Completed Y/N |
Comments |
Sign-Off |
Date |
System and database administrators, project managers, team leads, developers, and users are identified and understand their roles, responsibilities, and timelines
|
|
|
|
|
User accounts are configured in the production instance(s) with the appropriate privileges, and verified to work on their respective devices/platforms prior to go live
|
|
|
|
|
All required physical and virtual resources are budgeted and earmarked for use prior to go live
|
|
|
|
|
Communication and workspace plans are in place
|
|
|
|
|
Any customizations or deviations from standard product are known and assigned to specific developers, and have been signed off on by the customer
|
|
|
|
|
Training and Documentation
|
|
|
|
|
Users understand the basic project plan, naming conventions/terms, and where to go for assistance
|
|
|
|
|
Users have been trained on their tasks, best-practices, and responsibilities and have clearly demonstrated competence
|
|
|
|
|
Key users are ready to assist and support the implementation
|
|
|
|
|
All processes, including SOP, have been documented to agreed-upon standards and copies are available to everyone involved
|
|
|
|
|
Training materials are available to everyone involved and are designed to be updated as needed for future versions
|
|
|
|
|
Any RF function keys or other helpful shortcuts are documented and available as needed
|
|
|
|
|
Data Conversion
|
|
|
|
|
Data conversions have been performed and all of the master and transactional data are loaded and verified into the production instance
|
|
|
|
|
All transactions have been removed from the production instance
|
|
|
|
|
Data backup and database maintenance strategies have been agreed upon and tested
|
|
|
|
|
Cutover / Migration
|
|
|
|
|
Everyone involved agrees to the cutover plan and timeline
|
|
|
|
|
All open orders and receipts are closed and completed in currents system prior to go live
|
|
|
|
|
Any necessary rollouts or hotfixes have been applied in the proper sequence and according to schedule
|
|
|
|
|
Testing
|
|
|
|
|
Initial vendor and customer infrastructure compatibility and reliability check
|
|
|
|
|
End-to-end user acceptance testing has been performed, and the customer has signed off that all issues have been resolved and all connections between the WMS vendor and customer instances are verified working
|
|
|
|
|
Integration testing has been performed on the entire production system (including any involved ERP systems), and the customer has signed off that all issues have been resolved
|
|
|
|
|
Regression testing has been performed (preferably via an automated testing solution) on the entire production system for key user flows like receiving, putaway, picking, inventory management, and dispatch
|
|
|
|
|
Performance/Volume testing has been performed on the entire system using peak production volumes, and the customer has signed off that the response times are adequate
|
|
|
|
|
Hardware and Consumables
|
|
|
|
|
All workstations and instances have been identified and configured, and can connect to production instances
|
|
|
|
|
All report and label printers have been identified and configured, and have had at least several test prints performed
|
|
|
|
|
Any required RF devices, scanners, and scales have been identified and configured, and tested to read bar codes, and can connect to the production instances
|
|
|
|
|
Any required scanners and scales have been identified and configured, and can connect to the production instances
|
|
|
|
|
Adequate quantities of toner and/or label stock have been acquired to support printing reports and labels
|
|
|
|
|
Post Go Live
|
|
|
|
|
Any support personnel or other team members remaining on-site are known to everyone involved in the project
|
|
|
|
|
The support ticket process and review schedule has been communicated to everyone involved in the project
|
|
|
|
|
Success metrics and KPIs are in place to track the progress post go live
|
|
|
|
|
Disaster recovery/contingency procedures and business continuity plans are in place for worst-case scenarios, including a master inventory data reload option
|
|
|
|
|
All customer agreements (whether tied to service levels, performance, capacity, etc…) have processes in place to measure, manage, and track them
|
|
|
|
|
This post was written by:
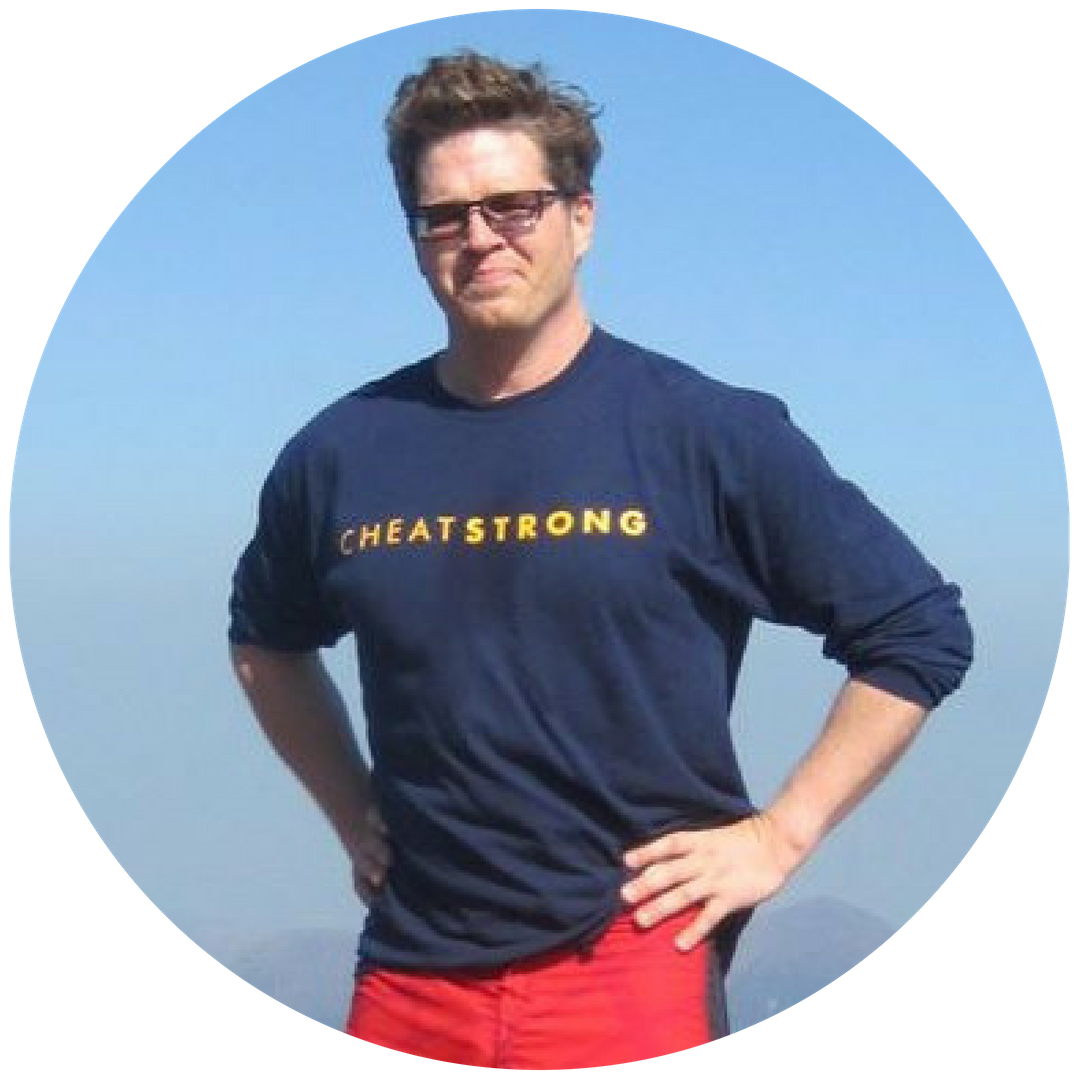
Recommended Content
SLA Optimization Worksheet
Enhance your service level agreements (SLAs) with this SLA Optimization Worksheet. Use it to assess your current systems, identify gaps, and create a roadmap for improvement. Includes actionable steps, KPIs, and next steps to boost efficiency and customer satisfaction.
Digital Transformation: The Key to Meeting Customer Expectations
In today’s fast-paced retail environment, customers expect seamless experiences whether shopping online or in-store. Shipped-to-home orders, in-store pickups, and last-minute changes are now the norm. However, many businesses struggle to meet these demands due to...
Tryon Solutions for Test Management
At Tryon Solutions, we design tailored Test Management strategies that help you proactively identify failures and streamline testing processes. Our expertise ensures your systems are reliable, safeguarding your operations from costly downtime. Download the brochure...
When to Hire a WMS Consultant
Your Warehouse Management System (WMS) is at the core of your supply chain operations. As the demands on your warehouse evolve, ensuring your WMS is future-proof is critical to maintaining efficiency, meeting customer expectations, and staying competitive. But when is...
Industry 4.0 Solutions that are Transforming Warehouses
The warehouse industry is transforming with Industry 4.0 technologies, shifting from traditional methods to innovative solutions that enhance efficiency, reduce costs, and improve productivity. These advancements go beyond automation, making warehouses smarter, more...